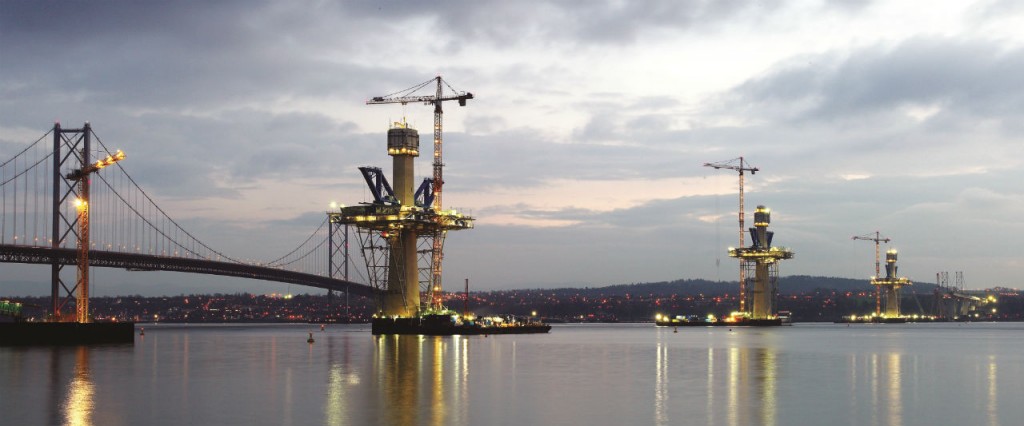
A world record is being repeated in Canada with the rebuilding of the Angus L. Macdonald Bridge which connects Halifax and Dartmouth in Nova Scotia. It is only the second time a suspended bridge has been replaced at night while traffic continues to flow during the day; the first time was the Lions Gate Bridge project, rehabilitated between 2000 and 2001, and featured in Heavy Equipment Guide at that time.
In Scotland, a different record is being set with the longest three-tower, cable-stayed bridge in the world, and the largest to feature cables that cross mid-span.
Angus l. Macdonald Bridge
The Big Lift is a $150-million project that includes replacing the road deck and stiffening trusses and suspender ropes on the Macdonald Bridge, which at 60 years old is showing signs of its age. Corrosion on the underside of the road deck, between the deck and the I-beams, has pushed the deck up, causing a bumpy ride for motorists. The corrosion has created an ongoing maintenance issue.
Two years ago Halifax Harbour Bridges tendered a contract to replace major parts of the bridge, with the winning bid going to American Bridge Company Canada, the same firm that restored the Lions Gate Bridge in Vancouver.
The two projects, and the two bridges, are nearly identical. Both were designed by the Montreal firm of Monsarrat and Pratley. Lions Gate Bridge opened in 1938 and the Angus L. Macdonald Bridge opened in 1955.
Once work is complete on the Angus L. Macdonald Bridge, the only original remaining bridge components will be the two towers, the main cables, the cable bents and the anchorages.
Replacing the 46 deck segments while still allowing the bridge to operate as normal requires a high level of engineering skill as well as logistics, since the construction schedule must accommodate bridge closures and openings.
The closures started on weekends but are planned for weeknights as engineers perfect the deck replacement process and get it down to a 10.5-hour window, allowing one segment to be replaced per closure. The work started on the Dartmouth side of the bridge and will proceed to the Halifax side, a process that is expected to take about a year. The first deck segment was replaced in October and by January 2016, at the time of writing this article, four segments had been completed.
Halifax Harbour Bridges often gets asked whether the suspended spans were replaced when a third lane was added in the 1990s. While the approach spans were replaced during that project, the suspended spans were not. To create the third lane, five feet of deck was added using the sidewalk and ductway. A new sidewalk and bike lane were added to the bridge outside the cables.
The segments are being replaced in 10- or 20-metre sections using a lifting gantry, which clamps onto the vertical hangers coming off the main bridge cable. Each segment contains a piece of deck, sidewalk, bike lane and water main that runs along the outside of the bridge.
Four strand jacks, manufactured by VSL International Limited, lower and raise the segments, which weigh up to 130 tonnes apiece. A strand jack uses a hydraulic jack to control a bundle of cables, or strands, as the load is lowered or raised.
Besides the lifting gantry with strand jacks, the Big Lift is also employing a number of pieces of lift equipment including dockside cranes, mobile cranes from Manitowoc (Grove RT540E and Grove TMS9000E), boom lifts from Genie (S120 and S125), a JLG 2032ES scissor lift and Genie GTH 1056 telehandlers.
The bridge deck is being cut into sections for replacement. The first 30 sections are being cut into 20-metre lengths with each section lowered straight down to a barge in the harbour and the replacement section then hoisted up and joined to the new span.
As explained by Jon Eppell, chief engineer with Halifax Harbour Bridges, the last 16 sections cannot be replaced in this manner because the HMC Dockyards lie below them on the Halifax side. These sections will be 10 metres long and need to be trucked across the bridge deck and rotated so that they fit between the main cables.
“They’re turned 90 degrees to the orientation we want them in. So what we do is we have the same lifting gantry, but we put a turn-table on it,” he said. “We’ll cut free an existing deck segment, lift it up, rotate it 90 degrees, put it on the back of a truck, haul it away, cut down the trusses so it will fit under all of the structure on the bridge. And then we’ll back up another truck with the new segment on it, lift it up, rotate it and lower it into position.”
The new deck, fabricated by Dartmouth-based Cherubini Metal Works Ltd., will be raised by 2.1 metres to accommodate large vessels including post- Panamax container ships that move through the Panama Canal. Currently there is only about a metre of clearance between the underside of the bridge and the largest vessels.
Once the bridge deck is finished, crews will move on to replace the vertical hanger ropes. The main bridge cable will remain, having been found to be in good condition, but will be wrapped and “dehumidified” in order to prevent corrosion and extend the life of the bridge beyond 75 years, according to Eppell.
Custom-designed cable crawlers, which inch along the main cable every few feet, will be used for tightening cable band bolts, replacing hangers and wrapping the main cable.
To check progress on The Big Lift, including a time lapse video and updates on closure times, visit the website at www.hdbc.ca/redecking.
Queensferry Crossing Bridge
One of the largest infrastructure projects in Britain is underway in Edinburgh. Liebherr, the Switzerland- based heavy equipment manufacturer, has been a key part of the project since its inception in the fall of 2011.
Once it is completed in late 2016, the 2.7-kilometre Queensferry Crossing will be the longest three-tower, cable-stayed bridge in the world, and the largest to feature cables that cross mid-span.
The bridge is being built across the Firth of Forth alongside the existing Forth Road Bridge, a 51-year old structure showing signs of deterioration. With a budget of around GBP 1.4 billion, the project is second only to Scotland’s largest-ever transportation project, the GBP 3 billion A9 Perth to Inverness roadbuilding program, which broke ground in September.
Bridge construction
Three Liebherr 630 EC-H 40 tower cranes were used to construct the three towers, designated as south, central and north. The towers range in height from 202 to 210 metres. Hollow steel caissons weighing up to 1,200 tonnes were sunk almost to bedrock, then filled with concrete using a concrete barge. The pours occurred in sections, with each pour raising the height of the tower by 4 metres. The cranes working on each tower were also raised, in 5.8-metre sections, eventually reaching a lifting height of 212 metres.
For the south tower, the volume of concrete poured underwater continuously amounted to 16,869 cubic metres – a world record.
Other interesting aspects of the bridge include: The bridge structure has an overall length of 2,633 metres including a cable-supported structure of 2,020 metres, the world’s second longest.
The bridge design includes 14 spans, three concrete towers, two planes of stay cables, and a concrete steel tub/concrete deck superstructure.
Approach viaducts will connect the access roads on either side of the crossing to the bridge deck. On the southern approach two 3,000-pound viaducts are supported by eight V-shaped piers, and stretch 543 metres over water to where the bridge deck begins. The viaducts are moved into place using cables that control the level of the deck as it is pulled over each pier.
Windshielding is expected to protect motorists from high winds in the Forth estuary and prevent bridge closures, which is a problem with the current Forth Road Bridge.
The new bridge will contain 23,000 miles of cabling – enough to wrap around the moon three and a half times.
The steel required for the bridge deck weighs 35,000 tonnes.
Liebherr 630 EC-H 40 tower cranes
According to Liebherr, the 630 EC-H 40 Litronic tower cranes were designed for the high winds common in the Forth estuary and engineered for the guying on the towers and the loads for the caisson foundations.
The company says one of the main challenges of the project was the capacity to handle 30,000 tons of steel, with some high individual loads. The cranes are equipped with a 36-metre jib and lift up to 180 tons at the jib head. At a radius of up to 18 metres, the cranes are designed for a 40-ton capacity.
“This configuration enables a particularly high-handling capacity with heavy loads. This lifting capacity is also supported by the 110-kW high-performance hoist gears which are in use on the project, and which guarantee fast lifting speeds,” Liebherr states.
Liebherr mobile and crawler cranes
Since the start of the project in November 2011, 12 different types of mobile telescopic and lattice boom cranes have been deployed on the site. Cranes from 400 to 500 tonnes have been used to lift components needed to construct the bridge. On average there are eight telescopic cranes on site each day. At least one model of almost every telescopic crane that Liebherr manufactures has been used on the project, according to the company. Smaller cranes are used for handling rebar, placing shuttering and carrying out general construction lifts. The larger cranes are called in to lift bridge deck segments and precast sections.
Two Liebherr LR 1300 crawler cranes have been deployed on the project. One is mounted on a barge situated in the river, which operates in support of the three Liebherr tower cranes. The second machine is based on the shore, and operates in support of the barge, loading out components that are taken to the base of the towers.
Company info
1015 Sutton Drive
Burlington, ON
CA, L7L 5Z8
Website:
liebherr.com/en/can/about-liebherr/liebherr-worldwide/canada/liebherr-in-canada.html