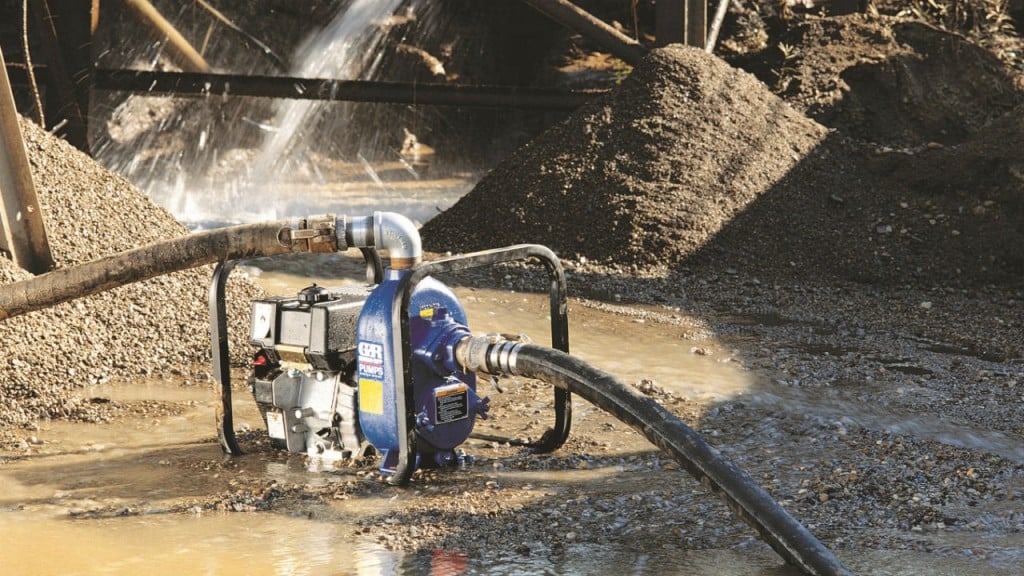
Second to motors, pumps are the most widely used mechanical piece of equipment and essential for many construction projects – including road works, drainage systems, high rise buildings, dams and bridges – where water flowing over the site can be hazardous and slow production.
Pumps come in various designs but can be summarized in two categories: positive displacement and variable displacement, both of which are commonly used on construction sites.
Examples of positive displacement pumps are:
Not all the above are used for de-watering but are used to pump concrete or transfer fuel, oil or other liquids.
The most common type of variable displacement pump is centrifugal. The centrifugal pump is widely used for construction site de-watering and comes in various configurations: end suction, self-priming, vacuum assisted and submersible, all of which are effective when applied correctly. Applying any equipment incorrectly most likely will increase the cost of ownership.
A common thought when using a pump is: the pump can run dry so let’s keep it running. When you consider fuel costs, hydro costs and maintenance costs – which are not declining – running the equipment without pumping any liquid is an added and unnecessary expense.
How to select a construction pump for de-watering
Planning pump selection is an important function. Once a decision is made to utilize either electric motor or combustion engine, the selection processes are very similar.
In order to effectively select a pump, the following needs to be determined:
For the installation, keeping the suction line submerged is recommended. This way the pump is pumping fluid and not air or a combination which wastes precious energy. Consider a valve on the discharge to isolate the discharge, test the integrity of the pump and provide back-pressure if necessary. A liquid level device can be considered to turn the pump on and off, keeping within the manufacturer’s recommendations. A further consideration could be to utilize multiple pumps for a variable incoming flow; these pumps might not necessarily be of the same size.
For more complex dewatering projects utilizing multiple pumps, multiple suction lines and multiple discharge lines, it is best to consult with pump/system professionals that can provide you with safe suggestions and instructions. Parallel and series systems can be complex but can also be very cost effective.
Maintenance and operation tips
1. Keeping a pump pumping, rather than snoring (sucking in air), will generally increase the pump’s life and be more cost effective;
2. Inspect the condition of the oil in the pump as this provides a good estimate for MTBF (mean time between failures), allowing preventative maintenance to be implemented;
3. Change the oil if contaminated beyond the manufacturer’s specifications;
4. Keep pump clearance between the impeller and wear plate to specifications to maintain peak efficiency and decrease wear;
5. Use gauge ports to measure the pump’s performance at various intervals;
6. Keep the number of starts per hour within the manufacturer’s recommendations;
7. If a vortex is occurring in the water at the intake, submerge the suction line further or increase the diameter of the suction intake by means of increaser fittings or a suction bell. A larger intake decreases the inlet velocity without changing the suction pipe size, allowing for lesser submergence;
8. Keep the suction line from getting plugged with debris. Don’t allow the suction line or the submersible pump to bury itself into the mud. Float the suction line or hang the submersible pump so that it does not touch the bottom of the pond. If plastic bags, sticks or leaves jam up the suction strainer, the liquid can’t get into the pump in an efficient manner. If you have a suction gauge on the self primer, a plugged suction will show higher vacuum. With a submersible, you will see less flow and a lower discharge pressure;
9. Watch the speed. Running a pump faster increases wear if there are abrasive particles in the fluid that you are pumping. Running at half speed can extend pump life as much as three times;
10. Changing the hose size can alter the performance of the whole system. It is not always necessary to change the pump; sometimes just the hose needs to be changed. With a variable displacement, centrifugal pump, the higher the pressure the lower the flow. If the hose is too small, causing a high resistance in the system, change to a bigger diameter hose and it will lower the resistance, resulting in increased flow. If there is insufficient resistance, you can create more resistance be either using a smaller hose or closing down the discharge valve.
Troubleshooting tips
If the pump is not discharging water:
1. Check to see if there is water in the sump, the area containing the water to be pumped.
2. Check if the pump has fuel or power.
3. Is the pump primed? Basically, all pumps need to be primed. Self priming pumps need water in the casing to prime. Vacuum assist pumps do not need water in the casing but use an external priming system; they still need to be primed in order to function. Although submersibles are under the water, they still need to be primed. If a vapour lock occurs, the pump will not be primed.
4. Is there a suction leak (the vacuum gauge will be close to zero)?
5. Is there a suction blockage (the vacuum gauge will be higher than expected)?
6. Is the discharge line broken or plugged (discharge gauge will register higher than expected if plugged and lower if broken);
7. Place gauges on the pump suction intake and discharge outlet. This shows what the pump is doing and is a terrific tool to troubleshoot the system.
Mike Cosgrove is Manager, National Training, at Gorman-Rupp Canada. The company offers assistance with pumping requirements, selection, repairs and maintenance through their dealer network, and offers application training and maintenance seminars tailored to the customer’s specific needs.