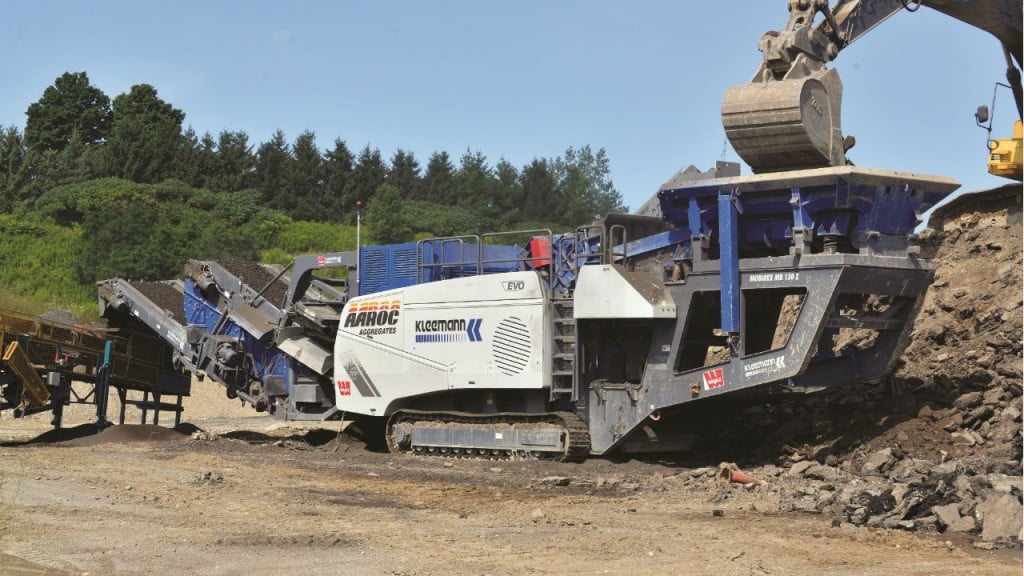
Today’s mobile crushers are rugged and dependable machines. Using correct maintenance practices, these machines will remain dependable throughout their working life.
Crushing and processing material can result in excessive wear on certain components, excessive vibration throughout the plant and excessive dust in the working environment. Some applications are more aggressive than others; a hard rock application is going to require more maintenance on top of standard maintenance, as you will get more vibration, more dust and more wear than from a softer aggregate.
From the moment a mobile crusher starts, the machine is wearing itself out and breaking itself down. Without routine, regular maintenance and repair, your mobile crusher will not be reliable nor provide the material your customers demand.
Feed system
Paul McLaren, a technical sales manager at Kleemann, offered advice on how to get the most out of mobile crushers.
He started with the first area of wear on any machine, the feed system. Whether it’s a feeder with an integrated grizzly or a feeder with an independent prescreen, how you feed the machine contributes to wear.
One of the major points to remember when setting up and maintaining a machine is that the machine must be level, he said. If the machine is not level left to right, this will cause increased wear on all components from the feeder to the screens, crushing chambers and conveyor belts. In addition, it reduces production and screening efficiency, as we are not effectively using the whole area of the machine. Also, having the machine sit high at the discharge end will have the effect of feeding the material uphill in the feeder and reducing its efficiency, thus reducing production.
Another area for consideration is the equipment with which the machine is fed. If you feed with a wheel loader, you have no control over the feed size as you can’t see what’s in the bucket.
With an excavator, you can see what’s inside the bucket and you have more control over the feed that goes into the hopper. You are not feeding so much material all at once and you are controlling the size of the feed, which reduces wear in the impact zones of the feed hopper and eliminates material blockages due to the feed size being too large to enter the chamber.
Grizzly
The standard integrated feeder is a grizzly section that is integrated into a vibrating feeder, so the feeder and the grizzly move at the same time. It’s a set of tapered fingers that allows material less than the size of the opening of the grizzly to drop through, bypassing the crusher.
This reduces wear on the crusher as material that does not need to be crushed never enters. That material is bypassed or sent to a side conveyor, but it is not screened to a classified saleable product. These grizzly fingers are a maintenance point and must be rebuilt and hard faced to maintain the sizing of material that you are removing.
Independent prescreen
The action of an independent prescreen is completely independent of the feeder. It also has the grizzly fingers at the top, or punch plate, but underneath material falling through goes through a woven wire mesh sized to any product the operator wants. Material not passing the mesh is bypassed around the crusher and discharged with the crushed product, thus reducing wear inside the crushing chamber.
In addition to maintenance on the grizzly fingers, we must also inspect the screen mesh for worn, broken or bent wires, and the seating face and tensioning devices for the mesh. As we want to obtain a screened product, it is critical to maintain the mesh so as not to allow material to fall outside of the required specification.
Thus, with an independent prescreen, product is screened in advance of the crusher, and it becomes an extra, classified product the operator can sell while the crusher is spared the volume of the bypassed sizes. For example, if you want a 2-inch product coming out of the unit, you don’t need to put any 2-inch material into the crusher. With an independent prescreen we can effectively remove any 2-inch-minus ahead of the crusher, because if you put any of that material into the crusher, it not only does not need to be crushed but it creates additional wear inside the crusher. Removing it also boosts production of material that needs to be crushed by the amount of material prescreened.
Fighting dust
Power unit
Dust is a problem in its own right, especially for the power plant of the mobile crusher. In a very dusty application, you can easily plug up your radiator, and you will have engine overheating problems.
High dust levels cause increased maintenance intervals on air filters, and if not controlled properly can enter the diesel tank and cause problems with your fuel system. Also, if you put that dust into the crusher, you increase wear. But if systems are put in place to remove the dust, you should not have it going into the machine in the first place.
Walkways and conveyors
Dust is also a hazard on walkways and a problem for conveyors. If maintained, side-skirting and sealing of conveyors keeps dust from spilling out, building up underneath the conveyor, or building up in rollers, pulleys, bearings, and causing wear on shafts. It’s important to maintain the sealing rubbers on the conveyor belts to avoid those issues. Routine maintenance calls for removal of accumulated dust from inside the machine and under it.
Electrical system
Dust also is a problem for circuit boards and programmable controllers used with modern machinery. Electrical systems under positive air pressure don’t permit dust to penetrate into the control system. Dust causes electrical switches to malfunction because it stops the contacts from correctly seating. In control panels with a correctly maintained positive pressure system, filters remove dust from air that is being pumped into the cabinets. If the filters are plugged, the system will not pull as much air through, allowing dust, moisture and heat to build in the cabinet.
Inside the crusher
The major wear part for a mobile crushing plant is the crusher itself. In a jaw crusher, the major wear parts are very limited: only a fixed jaw and a swing jaw, and two or four side or “cheek” plates.
An impact crusher, on the other hand, has a lot more wear items. The blow bars – which hit the rock and make it explode inside the machine – take a majority of the wear. We also have impact aprons against which the rock is thrown, which also see high wear. There are side plates or wear sheets on the sides of the machine. The highest wear area is around the impact crusher itself – around the circumference of the rotor. If you don’t maintain wear items, you will wear through and compromise the structure of the crusher box.
A daily visual check of the machine is recommended. The jaw is simple; just stand up on the walkway and take a look down inside. A jaw plate can be flipped so you have two sides of wear on them. Once half the jaw is worn out, you flip it; once that side is worn, you change it.
The impactor will have an inspection hatch by which you can see inside. How much material is left on the blow bars? How much is left on the wear sheets on the side of the crusher box? If after one week you’ve worn half the bar out, you know that you will have to change the blow bars in another week. The frequency of changes depends entirely on the application and the rock that is being crushed.
These are user-serviceable parts and the principles will be the same regardless of the manufacturer of your machine. They have to be user serviceable, user friendly, and able to be changed in a short time. The best way to change these parts is a service truck with a crane; we’ve seen people who use excavators but that’s not recommended by any means.
Managing conveyors
Conveyor maintenance – as with crushers – depends on the application at hand, that is, the hardness of the aggregate being crushed. If you are running a very soft limestone, you can get years from a conveyor belt that’s properly maintained, but one or two months from one that’s not.
With conveyors it’s really important to ensure it is tracking in the correct path, and not all the way over to one side, rubbing on the chassis. Make sure there’s no buildup underneath that can drag against the bottom of the conveyor, or catch on it and get dragged into the machinery.
It’s important to keep the side-skirting maintained; that will keep rocks from catching at roller stations and pushing down on the inside of the belt. No material should be caught in any part of the conveyor, whether it be the roller station, where material exits the crusher, or beneath the conveyor from spillage. Any of these will impact the longevity of the conveyor and belt.
If you don’t keep the conveyor clean, or keep the rollers working, the belt correctly tracking and the sideskirting maintained, the conveyor belt will be seriously compromised.
One design provides a vibrating chute beneath the crusher where material exits onto a conveyor. This takes a lot of wear away from the belt; instead of hitting the belt, aggregate hits the vibrating chute with steel wear liners. They are wear items but they can take a lot more abuse than a rubber conveyor belt. The impact is absorbed by the chute, which then feeds aggregate gently onto the belt to discharge to stockpile.
Clues to worn conveyor belts include worn rubber; patches of rubber that have been dug out, leaving holes in the belt where material gets caught; pieces torn off the edge of the conveyor belt; and tracks running the length of the belt, indicating where the rubber has been cut by a rock or piece of metal that has become stuck. Sometimes the cut will go all the way down to the reinforcement of the rubber belt. All these are signs indicating a belt that must be changed.
Wear of screens
Screens are obviously a vital part of the crushing and screening operation. Without the correct screen meshes, or with badly worn or maintained screen meshes, you will not get the product the customer specifies.
A standard woven wire mesh has a certain wire diameter. As it wears, the openings will become greater. We can go from a ¾-inch opening to 1-inch in size. That will cause the aggregate to fall out of spec, which can be critical, for example, to certain asphalt mixes.
Also, as the wire diameter gets smaller and smaller, the mesh becomes weaker and weaker, and is more prone to breaking. Instead of having one opening of ¾-inch, you will have an opening of 1 ½-inch by ¾-inch, and again, the material is out of spec. Look for worn and broken wires, and damaged crimps within the wire that are causing the screen mesh to move and allow larger material to pass through it.
Check the tension of the mesh. If the mesh is not tensioned properly, it will bounce around inside the screen deck and cause damage to the mesh itself and the surrounding screen box.
There are different types of enhancements that are purported to prolong mesh life. There is oil-tempered wire, non-oil-tempered wire and stainless steel wire. There are all kinds of meshes for all different applications. Some will reduce wear, some will reduce material sticking and blinding as it passes over. There are also selfcleaning meshes in different patterns. Choice depends on the application.
Training
While operational and maintenance training should be part of the initial commissioning of the plant, until the operator or a dealer comes to a formal training program sponsored by the manufacturer – away from the distractions of production – maintenance and service never can be truly optimized.
Maintenance of mobile crushers for optimum production is not only about when the task is performed but also how it is performed.
Unless the person making the checks has the training and knowledge to effectively take care of the machine, downtime will be increased and production decreased.
For optimum uptime, a thorough maintenance program – along with training of the operator and maintenance staff directly from the manufacturer – will ensure a dependable machine for years to come.
Company info
6030 Dana Way
Antioch, TN
US, 37013
Website:
wirtgen-group.com/america/en-us/products/kleemann
Phone number:
(615) 501-0600