Terex Washing Systems AggreSand 206 and AggreScrub 150 Integrate for Ultimate Flexibility
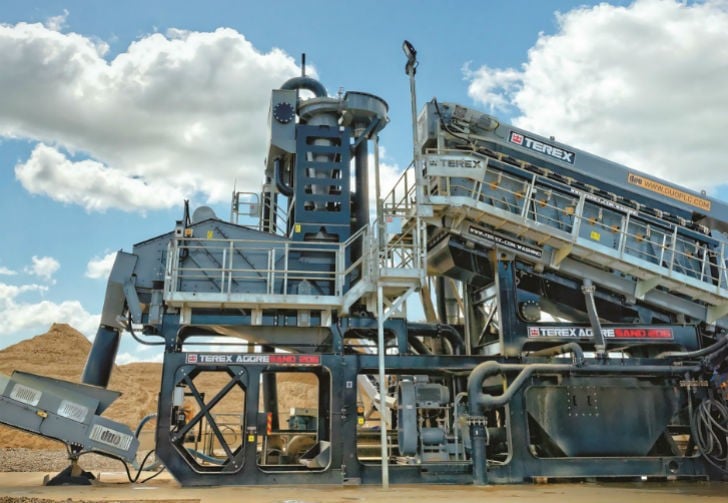
The world’s first seamless integration of the Terex Washing Systems (TWS) AggreSand 206 modular wash plant and the AggreScrub 150 is processing in excess of 350 tph, producing three aggregates and two sands, at a quarry in the U.K., owned by Lafarge Tarmac at the time. (Editor’s note: Lafarge Tarmac was purchased by Dublin-based CRH plc, effective August 1, 2015 and is now called Tarmac a CRH company. The use of the name Lafarge Tarmac refers to the company name at the time the story covers.)
The AggreSand concept, pre-wired and pre-plumbed with quick installation, was particularly intriguing to Lafarge Tarmac as a solution to their specific needs, far removed from other wash plant installations they experienced in the past. The material to be processed required scrubbing in order to produce a clean aggregate suitable for drainage, decorative stone and concrete production.
The AggreSand 165 model was originally selected and installed in June 2014 and had been producing thousands of tons of quality clean aggregate and two in-spec mortar and concrete sands. Lafarge Tarmac particularly liked the modular concept of the AggreSand; however, they required increased production to meet constantly growing demand.
When TWS announced details of the larger capacity AggreSand 206, as well as the AggreScrub 150, Lafarge Tarmac saw this combination as the next ideal solution for their specific requirements.
Double capacity
“This plant has the capability to process double the capacity of the previous fixed plant. It boasts a very innovative and compact design and gives us the ability, especially on sand production, to have ultimate flexibility, so we can make two sands at varying cuts. We have a 0-4 mm concrete sand and a 0-2 mm fine sand,” said Lafarge Tarmac regional operations director, Andy Bate.
Alex Moss, managing director for the distributor, Duo plc, commented: “This plant has allowed us to develop a solution with the client and work as one. Critical to this process was understanding what their specific demands were so we could bring to the table a solution to meet their requirements and variations. Acquiring information on their feed material, end-user and market demands was fundamental to develop a solution specific for them.
“The AggreSand 206 and AggreScrub 150 setup allows you to change with the market and you can very quickly move these plants from site to site if required. It is totally self-contained and has the flexibility to develop where you want to go as the market trends change.
“This plant is the ideal solution for sites that were previously not economically viable due to cost of penalties. This plant makes many more sites and materials bring value to the marketplace.”
The larger capacity AggreSand 206 plant is now installed and fully commissioned. The plant consists of a bespoke feed system which can either be fed by wheel loader via a 12-foot vibrating grid or by an existing land conveyor and radial feed conveyor. The feeder, including the vibrating grid, is electric hydraulically powered.
The main inclined feed conveyor, 23 metres long and 1,050 mm wide, is inclined at 18 degrees. It is driven by two 11 kW electric motors and Bonfigoli gearboxes mounted on either side of the drive drum. This setup not only provides balance to the conveyor but also gives enhanced torque characteristics. Lafarge Tarmac specified the use of Cooper split bearings on this conveyor for ease of maintenance.
The inclined feed conveyor has an integrated wash box, complete with spray bar which pre-soaks the feed material before it reaches the rinsing screen.
Three decks
The AggreSand 206 at Broom is a three-deck version which utilizes ten individually controlled spray bars on each deck. The two-bearing screen is fitted with polyurethane modular media on all three decks. The top deck acts as a protection deck removing any material above 80 mm. The middle deck is a 40 mm passing deck, while the bottom deck is split, 2 mm and 5 mm, to produce the required two sands. It is fitted with two ‘stumpy’ conveyors which deliver the over- and mid-size material to two 65- foot stockpiling conveyors. Chute-work on the AggreSand 206 employs the now well tested dead-box system which results in rock-on-rock setup, which is proving to give excellent wear properties.
The feed material at this site has a high sand-to-stone ratio which is why sand throughput approaches 350 tph. TWS provided an innovative solution using the AggreSand single-grade, 200 tph sand plant to produce the concrete sand while a TWS FM 120C is utilized alongside the AggreSand 206 to produce the masonry sand.
Currently the AggreSand 206 single-grade sand plant – which consists of one 45kW 250/200 pump and two G4-660 mm cyclones, is producing clean in-spec concrete sand.
The FM 120, which has a 200/150 30 kW pump and one G4-660 mm cyclone, is producing in-spec mortar sand. These two sands are produced on the split bottom deck on the AggreSand aggregate screen. A specially designed rubber-lined catchbox allows blending to take place so that an acceptable coarse and fine sand ratio can be achieved. The fine material is captured in one section of the two-grade catchbox and piped to the FM120C’s sump tank. The material between 40 and 80 mm is washed, stockpiled and crushed periodically. The material between 5 mm and 40 mm is fed to the AggreScrub 150 for scrubbing and removal of clay conglomerates. The material to be scrubbed is fed via a specially extended, 16 m conveyor which safely feeds this sticky material at 17 degrees to the AggreScrub 150.
Abrasive scrubbing action
The Aggrescrub 150 deals with stubborn clay-bound material which cannot be removed by rinsing or screening alone. It consists of an 8 m hull fitted with two rotating shafts with 30 mm abrasion resistant blades. The blades convey the material from the feed end of the scrub to the aggregate rinsing/sizing screen. As the material travels through the hull, the abrasive action of the aggregate as it collides with other aggregate (stone on stone) scrubs it clean and breaks up any clay conglomerates which are then floated off through the back of the AggreScrub. Any organics, such as roots or plastics, are also floated off to be dewatered over the AggreScrub’s 6x2 trash screen. Underflow from the trash screen is received in a catchbox under the screen and then gravity fed to the sump tank under the hull.
Scrubbed aggregate exits the main discharge of the AggreScrub 150 to a 12x5 part rinsing screen. The initial section of this screen is fitted with spray bars to rinse off any sand/grit residues produced during scrubbing. The rinsed grit is captured in a partial catchbox under the screen and is piped to the sump tank below the hull to join the trash screen underflows. This sump tank is fitted with a 100/100 centrifugal pump which pumps this dirty water back to the AggreSand 206 sand plant to recover any sand and make maximum use of internal water. The two deck 12x5 screen is fitted with polyurethane modular media to produce 5- to 10-mm, 10- to 20-mm and 20- to 40-mm clean aggregate. The three clean grades of aggregate are stockpiled using three TC6532 conveyors.
The control system for this specific AggreSand wash plant is located in a centralized cabin on the site. This is one of the options offered by TWS on all AggreSand units; alternatively the panel can be mounted onto the machine.
Miles Dobson, Head of Manufacturing, Lafarge Tarmac, commenting on this setup, said: “The fantastic thing about the AggreSand is the modular design, allowing us to be flexible and fast in the market – it allows us to react quickly and in many ways.
“We also have the ability to add a larger sand plant if the market changes. “It was a very swift installation, is running efficiently and is producing what we anticipated.”
Company info
200 Coalislad Road
Dungannon,
IE, BT71 4DR
Website:
terex.com/washing-systems/en/index.htm