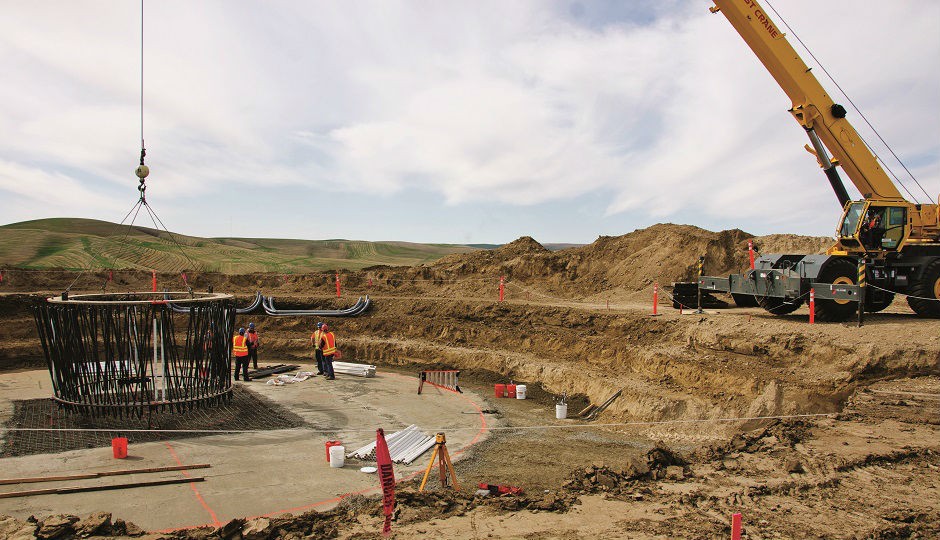
On a wind-swept ridge overlooking the Tucannon River, a tributary of the Snake River fed by snowpack on the distant Blue Mountains to the east, RES Americas Construction Inc. is leading the construction of a $500 million wind farm at a 20,000-acre site near Dayton, Washington. When completed, the Tucannon River Wind Farm’s 116 wind turbines will have a total generating capacity of 267 megawatts of electricity, making it Portland General Electric’s second largest renewable energy project. The wind farm is expected to produce an average of around 101 megawatts, enough to power the homes of about 84,000 residential customers.
Goodfellow Brothers is building 40 miles of new road for the project and preparing each of the sites for the wind towers and turbines. When completed, each wind turbine tower will stand 160 feet from the ground to the turbine motor, with three 110-foot blades.
Shipped from Europe, the massive parts of the wind towers and turbines arrive by boat in three sections and are loaded onto a train and shipped to eastern Washington, where they are loaded onto trucks to be delivered the last hundred or so miles to the wind farm.
“Everything must be coordinated,” said Richard Kornmann, visual inspection analyst for Goodfellow Brothers. “So, the road work and site preparation must all be completed on several tower locations before the erection crews arrive.”
Kornmann said when the parts start to arrive, installation of the towers must be done by three separate teams with different equipment. Each team is responsible for different sections. The first team installs the tower base. The second team installs the turbine and the third team installs the blades.
“Once the erection crews arrive on site, site preparation at each tower pad must be completed in a timely fashion so that the crews can continue their work and keep to their schedule,” said John Stump, equipment department manager for Goodfellow Brothers “The cranes used in the installation are very expensive to operate. Any delays on our part would result in hefty penalties against our company and we would lose a lot of money. There’s no room for error.”
Kornmann said Zonar equipment provides Goodfellow managers real-time information that they can use to monitor progress on the site preparations and to deal with any equipment issues that could potentially delay the entire project. And since managers can generate detailed reports that include engine hours plus vehicle speed, location and condition, they can provide RES Americas more detailed and accurate reports. “RES Americas places a great deal of emphasis on safety,” Korn mann said. “The maximum speed limit for all vehicles on the project site is 20 mph. There are no exceptions. And we must provide proof to RES Americas that we strictly enforce that speed limit at all times.
“Since the distance from one end of the wind farm project to the other is more than 15 miles, it can take anywhere from 45 minutes to an hour to travel from one tower pad to another,” he added. “That places even greater time restrictions on our on-site crew of 35 employees. If they run late, they can’t speed through the project to get to the next tower pad.”
“Having access to engine hours also helps us in monitoring rental units and PTO operations on trucks so that the company’s accountants can determine and claim any state and federal fuel tax reimbursements,” Kornmann said.
Installation time cut in half and connectivity improved
Recent advances made by Zonar have contributed to a vast improvement in connectivity, particularly in remote rural areas like the Tucannon River in southeastern Washington, Kornmann said.
“In these rural areas, we’ve seen an 80 to 90 percent improvement in reception,” he said. “This means that I have many fewer gaps in vehicle and vehicle inspection data.”
Recently, Goodfellow Brothers began upgrading to the Zonar V3R telematics platform, which features a newer generation of wireless technology than the company’s previous units. And Goodfellow has been installing newer wire harnesses from Zonar in its vehicles, which cuts the installation time of the telematics system in half from more than two hours to less than an hour. Since the V3R and the new wiring harnesses can connect to the onboard diagnostic (OBD-II) ports of most vehicles, Goodfellow Brothers managers could have access to an even greater treasure trove of data, particularly from its Ford pickup trucks.
“There’s no question that Zonar helps us save money through greater operating efficiencies,” said John Stump, equipment department manager for Goodfellow Brothers. “But what’s been really important to us is how Zonar has helped us to more closely monitor our vehicles and equipment so that we can remain the contractor of choice for our customers and our employees because we maintain a safe and efficient work environment.”