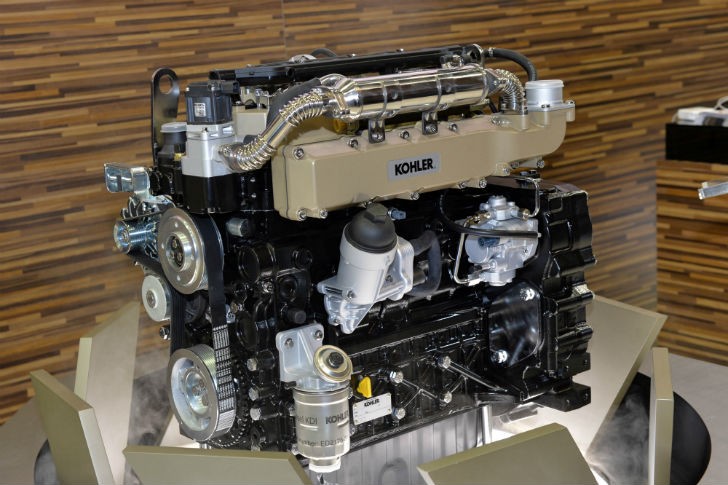
Kohler Engines, has launched the KDI 3404. The new 3.4 L engine that reaches 100 kW and 500 Nm despite its extremely compact size, with an innovative, “Stage V ready” after-treatment system.
The KDI 3404 model completes the platform of KDI diesel engines. The KDI series is a complete range from 30 to 100 kW, with 3 different engine sizes – the 1.9L the 2.5L and now the 3.4L too. The decision to use cutting-edge technology ensures all the models meet current emission standards without the use of a particulate filter. This is made possible by the high-pressure common rail injection system (2000 bar) offering extremely clean combustion when it is combined with four valves per cylinder, with G3S solenoid-type injectors for an extremely precise supply of fuel during the injection process and with the use of an electronically-controlled EGR valve for the recirculation of the right amount of exhaust gas, liquid cooled by a water/air heat exchanger.The range of KDI 3404 engines by KOHLER Engines is completed by mechanical versions that offer an excellent performance and are ideal for applications and markets where the emissions standards are less demanding.
The KDI packs a great performance despite its compact footprint
The KDI 3404 reaches 100 kW of power at 2200 rpm; similarly it reaches 500 Nm maximum torque at 1400 rpm. These values rank among the "best in class" in their target segment and are matched by their high torque reached at minimum rpm: the KDI 3404 reaches 412 Nm at just 1000 rpm, enabling demanding work cycles at low rotation speeds, and so reducing fuel consumption by up to 10% while significantly limiting noise levels. The perfect integration of the turbo, engine and electronic control unit guarantees an immediate response to variations in load, yet another benefit for productivity and operating fluidity, and enabling 15 % higher levels of machine productivity compared to leading competitors.
The KDI 3404 also offers maximum efficiency in terms of the cost of ownership: minimum guaranteed maintenance intervals of 500 hours due to clean combustion without the need for a particulate filter (no DPF).
The highly innovative design of the KDI
The new KDI 3404 by KOHLER Engines was developed according to the "best fit" principle, i.e. aiming to be "the best engine with a reduced footprint". Many technological solutions have been implemented on the new engine in order to reach this goal. The innovative injection system with a high-pressure common rail system 4 valves per cylinder, fixed geometry turbo and EGR valve, make it possible to reach standards of performance that are usually seen with higher displacement engines (specific power: 30 kW/L; Specific torque: 150 Nm/L) all achieved without the requirement for a DPF. As a result, OEMs can replace the higher displacement engines in their projects with versions that have a considerably smaller footprint to reduce consumption without necessarily redesigning their application or, in the case of new machines, designing smaller engine housings leading to improved operator visibility and better productivity and safety.
The lack of a DPF helps to increase both productivity for the end user, who no longer has to slow down the work cycle because of the regeneration process, as well as making installation easier as there is no longer any need to adopt expensive safety measures to counter excessive heat loss and prevent fire hazards.
The two lateral auxiliary power take offs (PTO) (SAE A and SAE B) are a further guarantee of versatility, engineered to deliver maximum engine power and simplify integration with the hydraulic system of the various applications, reducing the space taken up by the machines.
The "bedplate" architecture (crankcase and sub-crankcase) used for the engine block and its counter-rotating crankshafts also ensure minimum levels of vibration and noise.
The special design of the KDI 3404 makes it the slimmest engine in its class, particularly important for agricultural applications where engines are placed on the front axle and have to be compact size with less width to give farming vehicles a better turning radius Thus making maneuvering much simpler.
In configurations above 56 kW, the KDI 3404 engine complies with Stage IV - Tier 4 Final exhaust gas standards thanks to the use of SCR (Selective Catalyst Reduction) to abate the Nox in the exhaust fumes.The special SCR solution chosen by KOHLER Engines helps to underscore the “best fit” philosophy. The “all in one” SCR system contains the DOC (Diesel Oxydation Catalyst), the MIXING Pipe and the SCR in a single piece of equipment. The extremely compact footprint of the whole device and the possibility to fit it at any angle, greatly simplifies its integration with the machine.
KDI 3404: Stage V ready
The KDI 3404TCR-SCR is already "Stage V Ready". The innovative and compact “all in one” SCR system has been designed so it can accommodate the DPF, currently the only technical solution capable of meeting the requisites for the number of particles of particulate in the proposed law currently in the process of assessment by the European Commission.
In the KOHLER Engines engineering layout, the “all in one” module will simply have to be replaced with a new module. The size is exactly the same as the previous one. This solution means that customers will not have to change anything in their application.
The DPF used will be small and its use will benefit the already clean combustion, thanks to the current injection system this will consequently have a lower number of regenerations than any other DPF while maintaining high levels of productivity.