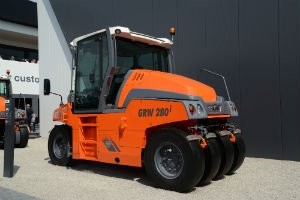
The new GRW 280i series of pneumatic compactors from Hamm incorporates Tier 4-interim emissions technology in a variety of weights for every application.
The GRW 280i updates the popular predecessor with subtle design changes and new engines complying with EPA Tier 4i.emissions controls.
While each model can be acquired in its own weight, the revised ballast compartment allows users to vary the operating weight even more easily and flexibly than before. New technical details include prefitting for its high-speed tire inflation system, and a standard oil service valve for lossless oil change ensures improved environmental protection.
Hamm’s new GRW 280i rubber-tired roller platform offers excellent compacting quality, plenty of driving comfort, extraordinarily good visibility conditions, and the highest of safety standards.
For the first time ever, viewing channels in the frame structure offer a view of the edges and the tires of the outer wheels. What's more, a novel suspension of the front wheels allows for an uninterrupted view towards the front.
The new GRW 280i’s operator’s platform rests in a versatile position, on a newly designed, asymmetrical frame. Innovations with respect to ballasting, drive concept and operating philosophy are not visible from the exterior, but their effects are evident as they make compacting better and more convenient.
A single driver’s seat – which can be moved and pivoted at the side towards the machine's outer edges and along with the console – has replaced two seats, two steering wheels and two control consoles in older models, which could restrict freedom of movement.
Operation and display elements are positioned on the console, and thus always are in the driver's field of vision. Also, the speed is no longer controlled by an accelerator pedal in the foot space; in the GRW series it’s controlled by joysticks, which signifies a considerable boost in convenience for the driver. In total, this operating concept corresponds to that of a tandem roller. Thus, cost-effectiveness is increased because in the future, operators can switch flexibly between roller types without any adaptation time.
Higher Speeds for Transport, Compaction
A hydrostatic rear-axle drive for the GRW 280i allows for higher speeds during transport and compaction. To match it, the newly conceived steered axle at the front with disk brakes – which is standard on all models 20-ton and over – ensures the necessary braking force and thus considerable safety when braking suddenly, even with maximum load. In total, sensitive control of the rear axle and an extraordinarily good view of the site and the wheels' edges enable high compaction quality.
The operator’s platform – with enveloping ROPS – is located in front of the center of the machine, while the Deutz 114-hp, Tier 4i-compliant engine is situated in the rear of the machine. This provides an excellent view of all relevant points. The view of the area directly in front of the front axle also is unobstructed. There, hydraulic cylinders for level compensation of the front suspension used to protrude out of the frame into the driver's field of vision. They have been replaced with two swing arms between the front pairs of wheels, which require very little space and are not visible to the driver.
The track offset between the front and rear wheelsets is one of the basic features of pneumatic rollers. Hamm utilized this fact in the design of the new GRW and designed the machine frame in symmetry with the wheelsets. This intelligent design offers one crucial advantage because, for the first time ever, the driver can see the wheels on all outer sides. Moreover, viewing channels in the frame structure offer a view of the tires of the outer wheels.