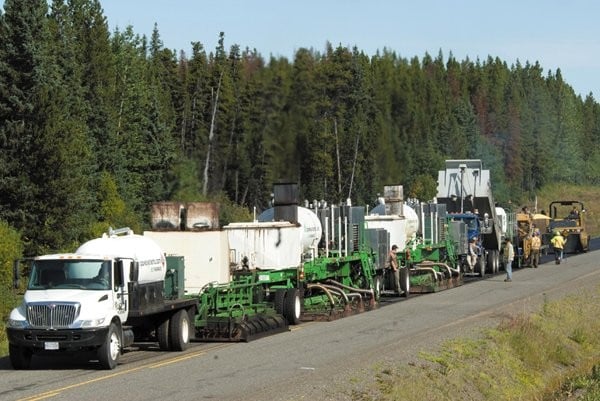
The Ecopaver 400 is a cutting-edge, asphalt recycling system which takes asphalt from existing roads and highways that are badly in need of repair and reuses it without shipping the asphalt to be refined off site.
The process was developed by Ecopave Systems Inc., a wholly owned subsidiary of Pyrotech Holdings Corp. The company pioneered the two-stage, hot-in-place asphalt recycling business and is the only manufacturer of the Ecopaver 400 two-stage hot-in-place asphalt recycling system.
The company claims that the machine is not only cheaper than other road recyclers and conventional paving methods, but it is also more efficient and far cleaner.
Less expensive and quicker
One of the Ecopaver’s signature benefits comes down to price. On average, it is 30-60 percent cheaper than conventional mill and fill methods and boasts an 80 percent reduction in non-renewable aggregate and oil requirements.
“Hands down, this is one of the most cost effective machines on the market,” says Al Rorison, the Ecopaver’s inventor. “For anyone looking to recycle the millions of gallons of oil locked in our roadways in an effective and inexpensive way, the Ecopaver 400 is a no-brainer.”
The entire recycling process also tends to be far more efficient than conventional repaving. The Ecopaver is able to recycle up to 2 ½ miles of one lane highway per day. Unlike conventional methods, traffic disruption is kept contained to small sections of road. On average, it takes 30 to 45 minutes from start to completion to pave a section of road. This makes the process generally safer than traditional methods, requiring fewer signs and controllers to reroute traffic. It also reduces inconvenience to the travelling public and adjacent properties.
“One of the biggest advantages our machine brings to the table is its ability to mill and recycle asphalt to twice the depth of competitors,” says Rorison. “This means we’re faster and more efficient than any other hot-in-place machine out there.”
The speed with which the Ecopaver is able to recycle sections of road recently made it an attractive option for the Federal Highway Administration. They were looking for a contractor who could help them pave stretches of highway running through Yellow Stone National Park. The challenge would be to recycle the road in the summer during the height of tourism season when roughly 115,000 people are driving through to visit.
Rorison thinks part of the reason the Ecopaver came up as a top option was its ability to pave with minimal disruption to drivers.
Greener
The machine is equipped with a powerful emissions control system, specifically designed to capture and cleanse any noxious gases or oil fumed smoke produced from the milling and heating of the pavement. The process reduces 50 percent more hydrocarbon emissions than traditional mill and fills methods. It is virtually smoke free and has one of the most advanced and effective collection and incineration systems on the road today.
In addition to its emissions control system, the machine also has the ancillary benefit of eliminating the need to haul in countless tons of new virgin asphalt. The Ecopaver recycles 100 percent of the existing asphalt. During the process the Ecopaver adds an additional 20 percent virgin asphalt to the road. This means 80 percent of the transport trucks used for conventional paving to carry virgin asphalt from the plant to the site are no longer needed. This not only decreases the cost of the paving project but also takes trucks off the highway and decreases carbon emissions.
Ecopaver method
The two-stage, hot-in-place asphalt recycling system uses a train of machines (a preheater, two self-propelled heater/miller units and a pugmill) to strip off cracked and old asphalt and recycle it, saving non renewable resources like aggregate and oil, as well as time and costs.
The first step in this process is the preheater, which is used to remove the moisture and heat on the top of a road or highway. The preheater utilizes propane fired high air flow burners and is equipped with an emissions control system, which incinerates unburned hydrocarbons and pollutants.
Next, the machine’s two-heater millers use tri grinders, which allow milling in widths of 10 to 14 feet and are equipped with automatic grade controls. The heaters utilize clean burning propane fired infrared heaters, are self propelled with all-axle steering, and feature a computer controlled rejuvenate dispensing system. The B unit heater is equipped with a drag slat conveyor to pickup the windrow from the A unit and transport the material over the heater beds. The heater-miller units mill up to two-inches depth of asphalt.
The final stage of the process is the pugmill. Inside the pugmill is a hopper, which is used to receive new admix. It is equipped with a drag slat conveyor, which picks up the recycled material and deposits it in the pug mill to be mixed with new admix. The material is then elevated to the pugmill’s hopper, which adds rejuvenates and mixes the virgin asphalt and the milled asphalt. It is then deposited into the paver hopper and spread back on the road or highway.
The recycled asphalt laid has the same qualities and life expectancy as virgin asphalt.