Astec redesigns highway-class Roadtec pavers
Streamlined look, stronger undercarriage, reduced noise & better visibility modernize 8- and 10-foot models
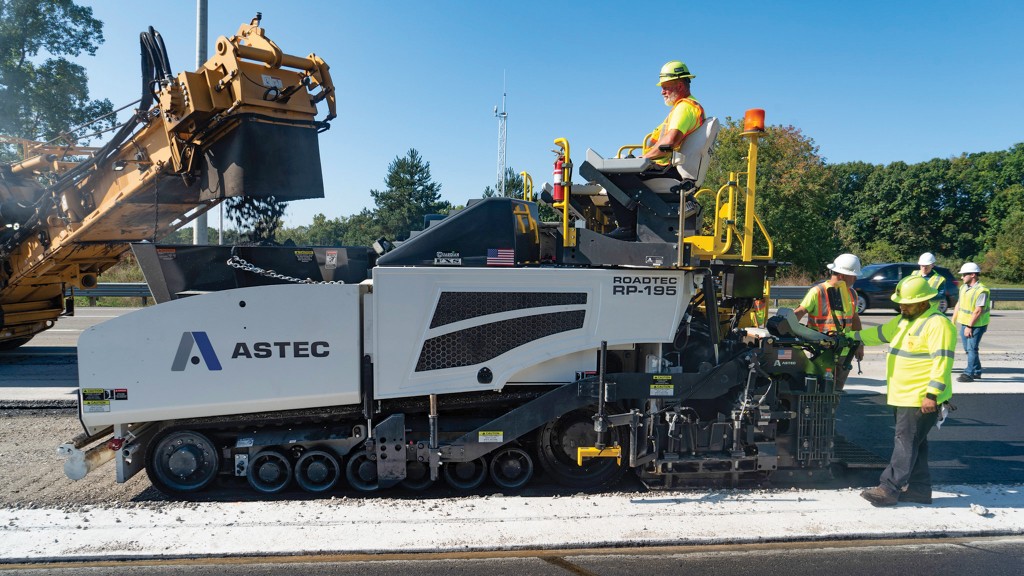
Astec Industries started a refresh of its Roadtec pavers in 2023 with the introduction of two updated machines, the 8-foot RP-175 and 10-foot RP-195 F-series. The overall look of these tracked highway-class pavers has been updated, and design changes emphasize uptime and operator safety.
Astec recognized several areas where the highway-class machines could be modernized and strengthened, according to Keith Hagy, product manager, Paving – Infrastructure Solutions. The overall look of the pavers became a starting point.
"Historically, we have focused much more on optimizing the function of the machine over design – we haven't really changed the look for many years," Hagy says. "The first thing you'll notice with our F-series pavers is more of a streamlined look when you see the side profile of the machine."
Design change adds undercarriage reliability and easier maintenance access
Astec identified design opportunities in the undercarriage that would improve reliability and reduce customer downtime. The undercarriage, initially designed as a multi-piece weldment, has undergone a transformative shift to a two-piece solid casting track frame, greatly streamlining the production process while strengthening the overall durability of the F-series.
This approach significantly minimizes weld points throughout the machine. "The result is a streamlined undercarriage structure that greatly reduces maintenance requirements, ensuring more reliable and efficient operation for our customers," Hagy says.
It also adds commonality between the 8-foot and 10-foot platforms, providing further production and service efficiencies across the F-Series platforms.
The new body design is not just an aesthetic update, but also reduces weight and gives users better access to key components. Composite materials are used for the hood and side panels, so operators will no longer need a hydraulic pump and lifts to raise the hood. This makes it easier for operators to check fluid levels daily, while side panels can be easily opened to access service points and filters.
Greater visibility is incorporated into the new design. Operators can see straight to the front of the hopper and with swing-out seats can gain a full view of the screed and head of material in the auger. Brightly coloured handrails and stairways help users quickly recognize where the safe access points are on the machine.
Both pavers have been updated to full Stage V / Tier 4 Final Cummins engines. The RP-175 is fitted with a new four-cylinder engine as opposed to the previous six-cylinder unit, a move that Hagy expects will provide higher fuel efficiency.
Noise reduction from relocated cooling system benefits crew health and safety
A new location for the cooling system is part of the design overhaul. Previously mounted on one side of the machine to pull air across the engine, it has now been placed on top of the engine, pulling air in from both sides and out the front of the machine away from the operator.
While efficient, the old design was also noisy, which customers had pointed out, Hagy says. Workers on the exhaust side of the machine were exposed to more noise, and the operator faced vibration and sound pushing back. The new approach lowers noise significantly, creating a safer working environment for the operators.
"Learning what our customers have to say about our machines is an important step in the innovation process at Astec. We listen to our customers, and what we heard is they wanted it to be easier to hear each other out in the field," says Hagy.
Astec further reduced noise levels by moving the generator from the screed to the engine compartment. "If you're the screed operator or the ground guys, you're hearing the generator continually when it's on," Hagy says. This relocated generator is larger, to ensure there is no loss of capacity, and has a more efficient direct-drive connection to the engine.
Overall, those changes have cut down noise from the pavers by about 20 percent, depending on the location around the machine.
Field testing of the RP-175 and RP-195 F-series pavers has proven positive, and Hagy says he is excited for machines to reach contractors in time for the spring.
"We're excited about spring startups, with all the machines getting out," he says. "We have put a lot of focus on operator comfort and safety – we're really proud about that."