Taking rock crushing to the next level
Automation technologies deliver higher productivity, lower cost per ton and greater safety
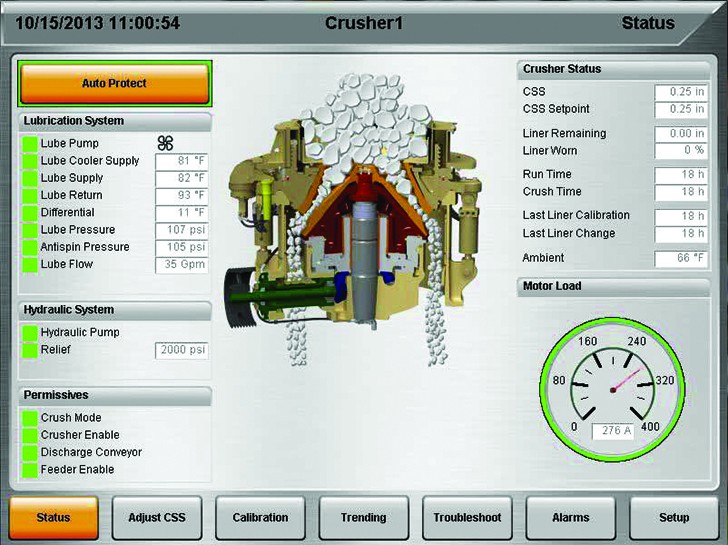
Using the right cone crusher automation system optimizes and protects the machine and allows integration into the network of any plant controls system, old or new, regardless of type or brand. This makes it easier for plant automation engineers and maintenance personnel to focus on controlling the flow of the entire plant, while knowing that the cone's automation program is doing its job.
Automated control systems for cone crushers provide a number of benefits which ultimately result in higher productivity, lower costs per ton, and increased safety.
"If you're not utilizing your crusher to its fullest extent, it's like wasting capital by buying a machine that's too big. We want an operation to ‘run right up to the edge' all day long without damaging the crusher. The automatic protection system on the controls package allow you to do that as it monitors horsepower, and protects the machine from upper frame bounce or high motor load," said Telsmith Engineer Shamus Coughlin as he explained the design features of the latest version of TRAC10, which is Telsmith's automated controls system for its T-Series Cone Crushers. The system includes the ability to run up to four crushers with a single touchscreen, as well as the capability to connect to the system via a Wi-Fi hotspot and laptop, or with a smartphone.
Coughlin said that the Telsmith engineering team has designed its controls system based upon the latest digital advancements and the need to provide solutions that optimize utilization. For example, he pointed to a new auto-power feature that automatically maintains the desired horsepower level on the crusher, while an auto-wear feature automatically tracks liner wear and makes closed-side-setting adjustments on the fly without the operator having to input anything. Also, the system allows operations to run at an optimal closed side setting. "There is enough protection provided on the machine that operators can run at a tighter setting and get...more in production without damaging the machine. Without automation, you don't have the data to know if it's safe to run it tighter, so the operation stays in what they know is a safe setting," he said.
In order to track liner wear, it's necessary to periodically calibrate the cone crusher, said Coughlin. Calibration is quickly completed by allowing the hydraulic anti-spin system to detect a zero setting. Upon each calibration, liner wear is calculated, allowing the system to provide warnings when liner wear reaches 50 percent, and then in increments up to 100 percent. "Also, the system takes calibration to the next level by trending what the average wear rate is over many calibrations," he added.
Among a number of screens on the touchscreen control panel is the crusher status screen, which is considered "mission control" for the system and provides the management of the crushing circuits. The status screen provides data on the lubrication and hydraulic systems, crusher settings, percentage of liner wear, operating hours, and links to other informational screens. Data is stored on an 8G USB, and the PLC stores one year of data per machine.
As the system is based upon the Ethernet Powerlink protocol, digital communication is reliable and in real time, which is its biggest benefit, said Coughlin. "All the data from the crusher comes back to the PLC over Powerlink, and the more real-time that data is presented to the PLC, the better that we can optimize and protect the machine."
With this level of automation on a crusher, operations can get remote access from outside the pit or mine. They have access to troubleshooting from the manufacturer, or they can pull data off their memory card at the crusher and easily troubleshoot at the facility.
Importantly, Coughlin said that the TRAC10 system allows integration into any plant. "No matter what the network of the plant, our system will be able to ‘talk' to their system," he said.
Typical components
A typical system is comprised of a Programmable Logic Controller (PLC) Panel; an Ethernet Communication Hub; an Ethernet Network; an Operator Interface Terminal (OIT); and a Crusher Panel.
The PLC is where the base program resides and where all the calculations are made. Hardware connections are made to motor starters that supply or receive instructions from the PLC. The PLC and the communication devices are supplied in an enclosure for mounting inside the motor control room. The Ethernet Communication Hub is located inside the PLC enclosure.
Located inside the operator control room, the Operator Interface Terminal (OIT) or the control panel is a touchscreen crusher operation unit. All trending data is stored in the unit on a memory card.
The Crusher Panel is located at the crusher lube tank. It centralizes the communications from the many crusher sensors and routes them to and from the PLC, which is located in the motor control room.
To make automation work, there must be a commitment at the top, and an eventual buy-in at all levels of the operation. The appointment of an in-house company systems specialist and a close relationship with the manufacturer will pave the way for ease of transition, overall acceptance, and a successful automation program that leads to higher productivity, lower costs per ton and zero harm.