Survey documents asphalt industry success in sustainability
Incorporation of recycled materials and energy savings of warm-mix asphalt technologies boost sustainable operations
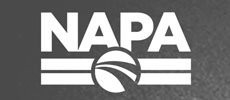
The latest survey of asphalt pavement mix producers documents the industry’s continued success in improving the sustainability of America’s roads through the incorporation of recycled materials and the use of energy-saving warm-mix asphalt technologies.
According to the latest survey of asphalt mix producers conducted by the National Asphalt Pavement Association (NAPA) in partnership with the Federal Highway Administration (FHWA), more than 77.2 million tons of recycled materials — primarily asphalt pavement material reclaimed from old roads and parking lots and recycled asphalt roofing shingles — was used in new asphalt pavement mixtures during the 2015 construction season. In addition, nearly a third (32.8 percent) of all asphalt pavement mixture was produced that year at reduced temperatures using warm-mix asphalt technologies.
The survey has gathered annual data from asphalt pavement mix producers and state asphalt pavement associations since 2009. Over that time, it has documented growth in the use of both warm-mix technologies and recycled materials in pavement mixtures. For the 2015 construction season, the survey was extensively revised to collect additional information about how reclaimed asphalt pavement and shingles are used nationwide.
“Asphalt pavements are already recycled at a greater rate than any other material,” stated Dan Gallagher, 2017 NAPA Chairman and Vice President of Gallagher Asphalt Corp. of Thornton, Illinois, “but we are not content with that. We continue to seek out and put to use practices and technologies that deliver high-performing roads, both in terms of drivability and sustainability.”
The survey found that more than 74 million tons of reclaimed asphalt pavement (RAP) and 1.9 million tons of reclaimed asphalt shingles (RAS) were used in new asphalt pavement mixes in the United States during 2015. An additional 7 million tons of RAP were used as aggregate, cold mix, and other road-building activities. The survey also found that at year-end 2015 about 85 million tons of RAP was stockpiled for future use across the country.
Reclaiming and reusing the asphalt cement and aggregate in RAP and RAS saved about $2.6 billion in 2015 compared to the use of virgin asphalt binder and aggregates. This helps keep asphalt pavement mixture costs competitive and allows road owners to achieve more roadway maintenance and construction activities with limited budgets.
Producers were also asked about ground tire rubber, steel and blast furnace slags, and other waste materials repurposed into pavements. Although national estimates of their usage were not calculated, respondents reported using more than 1.1 million tons of these materials in 2015 in the production of about 8 million tons of asphalt pavement mixes.
In addition to increased use of recycled materials, asphalt mix producers continue to increase the use of energy-saving warm-mix asphalt technologies. In 2015, 119.8 million tons of warm-mix asphalt was produced — nearly one-third of total asphalt pavement mix production. This is a 5 percent increase from 2014 and a greater than 614 percent increase in the use of warm mix since 2009, the first year the survey was conducted.
Warm-mix asphalt is produced with a range of technologies that reduce the production and placement temperature of asphalt pavement mixtures. A variety of environmental, worker safety, and construction benefits have been realized through the adoption of warm-mix asphalt. In 2009, FHWA selected warm-mix asphalt as one of the first technologies targeted for deployment through its Every Day Counts initiative.
“The use of warm-mix asphalt technologies is becoming commonplace. In 14 states, more than half of all asphalt pavement mixtures were produced as warm-mix asphalt, and in four of them, more than 75 percent was produced as warm mix,” stated NAPA President Mike Acott. “This said, there is room to increase its use, and we expect road owners to continue to embrace these technologies for their construction and performance benefits, as well as the energy savings they bring.”