Handling the Big Digs
The Anchor Shoring group of companies started as a two-family operation in 1968 and has grown to become a major player in the Ontario foundation construction business
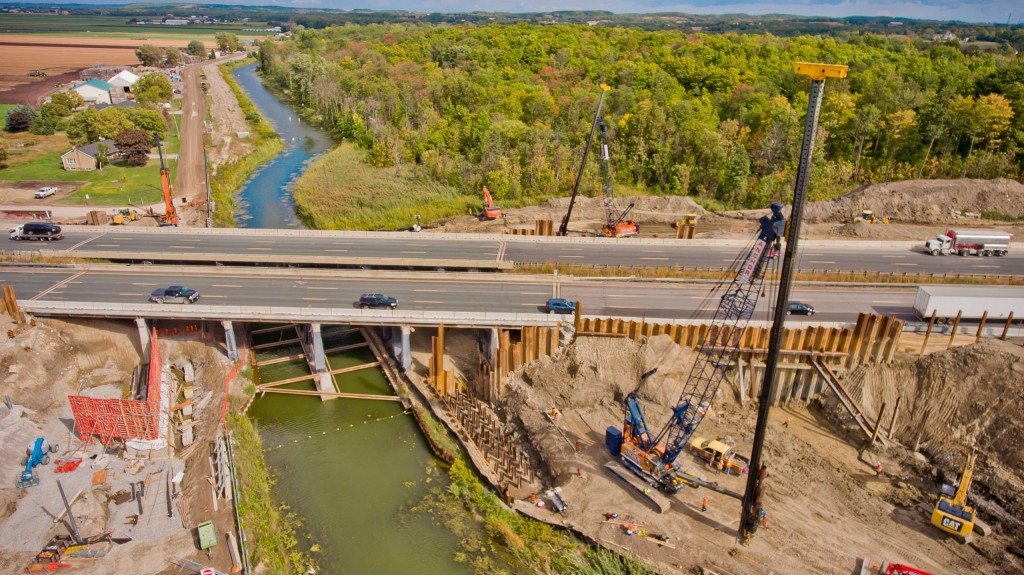
Southern Ontario is a challenging environment for construction companies to operate, due to soil conditions, water tables and the general busy nature of the region. When the company’s business is focused on shoring, piling installation, and other foundation-related construction, those conditions become even more challenging.
The Anchor Shoring group of companies has been meeting those challenges for nearly half a decade in the Toronto area and elsewhere in Canada. With a focus on getting difficult jobs done safely and correctly, the group has expanded steadily since its start as a one-machine operation, and today is capable of handling some of the most advanced construction projects in the region.
The group, made up of Anchor Shoring & Caissons, Banner Piling & Excavating, and Crown Drilling, got its start in 1968 thanks to two families and one drill, said Derrick Speakman, Anchor Shoring vice president.
“There was Gord Demetrick and Gord Stack, who had worked at a different company called Western Caissons, and decided that they could do this on their own. So, they started Anchor Shoring in March of 1968 with one drill machine and a three or four man operation,” Speakman said. “From there it kept growing , and was entirely organic growth. There were no mergers or acquisitions; it was just buying a new rig, hiring a new operator, bringing on another project manager.”
Through the nearly five decades since, Anchor has grown to have a staff of around 150 in total, much of it unionized. While the company was purchased by Green For Life (GFL) in January of 2016, the family connection remains – its president is Dawn Tattle, who is Demetrick’s daughter, and Stack’s grandson Matt is vice president and operations manager.
“Matt’s father Tom just retired when we sold the business – so there’s three generations of Stacks and two generations of Demetricks,” Speakman said. “I joined the company in 1987 – I’m not family, but I have 30 years here.”
Anchor Shoring has worked in many parts of Canada but has always had a focus on work near home in the greater Toronto area.
“We have done work across Canada and even outside of Canada – we’ve done work in Cuba over the years, for example,” Speakman said. “We are fortunate to be primarily an Ontario-based contractor. Our guys sleep in their own beds about 90 percent of the time – in our industry that can be unusual.”
While working near home may be a plus for the Anchor crews, the unique challenges of southern Ontario add difficulty for piling and shoring contractors. The province’s geology lends itself to a wide range of soil conditions that make planning and execution of foundation work a chore, especially when combined with dense urban areas.
“In Toronto, you can go from all fill material, where they’ve filled in the lake along the waterfront with rocks mixed into it, to wet sand, to hard clays, to everything in between,” related project manager Dave Winter. “Just going across the city can be a whole different ball game sometimes. A lot of work we do is on highways, and sometimes they’re near buildings – depending on the soil conditions, that can bring even more challenges.”
Working in areas with a high water table – which can encompass much of the Toronto region – allows Anchor to demonstrate its talents, Speakman said.
“Having a high water table sometimes separates the stronger contractors from the others – we think we have the right equipment and the right manpower to do it,” he said. “The more challenging the job, the better we like it.”
In the shoring sector, which for Anchor is focused on drilling, the industry has seen many changes over time thanks to advancing technology, Speakman said.
“The machinery, in the last ten years, has changed drastically from the first part of my career,” he said. “Everything used to be mechanical drilling machines – chain-driven, belt-driven machines with what we considered high torque powers at that time. But in the last ten years, hydraulic machines from Europe, from manufacturers like Bauer and Liebherr, have come in. The energy and torque that we can get from those machines is double or triple what it was in the past. They’re quieter and far more productive.”
For Winter, whose expertise lies in the pilings side of the business, key advancements have focused on the length of piles that can be used and placed on job sites.
“The main thing that’s changed is the length and capacity we can get out of piles. Engineers are now asking for higher loaded piles, which has in turn increased the size and length of them as well,” he described.
Anchor has a Kobelco 160-ton pile driver that can install 115-foot piles in one length, rather than having to use multiple splices to reach the needed depths, said Speakman.
“One hundred and fifteen feet is the size of a ten- or 11-story building – the logistics of that is incredible. Just getting the steel fabricated in that length at a mill is a challenge,” he said. “Then you need a special truck to get these long beams to the job site, unload them and install them.”
Similar to the drilling side, hydraulic machines and larger equipment have moved in to the pile driving sector, though it continues to remain one of the more simple operations on a construction site.
“Pile driving is one of the oldest forms of construction, and it really hasn’t changed too much over time,” Winter said.
What has changed is the way in which pile driving contractors must work within the constraints of the ever-changing urban landscape. More restrictions on noise mean more challenges for the operation, noted Speakman.
“There are so many restrictions with regards to noise and vibration concerns. The density of Toronto doesn’t really allow for a lot of pile driving to take place,” he said. “We don’t go around damaging structures by pile driving, but there is nobody here who would say it’s not a nuisance.”
Today, pile driving is often used more on large infrastructure works such as sewage treatment plants, bridges and other large projects in less crowded spaces, while hydraulic drilling is used in other areas.
With a skilled staff and extensive array of equipment, it’s no surprise that Anchor Shoring has tackled many difficult jobs in the Toronto area – and, in some cases, very big jobs in more ways than one.
The Zone 1 watermain was a recent construction project in Oakville, just outside Toronto. A major project for the region, the proposed construction method required an entry shaft to be constructed to allow for a tunnel boring machine to be extracted. The problem: the shaft was huge, deep and had to be bored through Ontario bedrock.
“The client needed a shaft that was 150 feet deep, and fifteen and a half feet in diameter – and we drilled it, as opposed to conventionally shoring something and going in with a small excavator and crane, which would cause the shaft to be much larger in diameter,” Winter said. “The client really liked the solution we provided because it saved time and money.”
Anchor brought in a Liebherr LB 44 drill rig for the two-month project, which was the largest diameter hole the company had ever done.
“The biggest we had drilled prior to that was a 12-foot diameter – it doesn’t sound like the extra three and a half feet is much bigger, but the tooling required and the setup of the machinery is on a scale, and this was roughly doubled,” Speakman said. “We needed a police escort to move the auger – it was wider than the lane of traffic.”
As for the shaft itself, the depth was such that when Anchor’s team was drilling towards the bottom, it took seven minutes to bring the auger back up for soil removal, Speakman noted.
With the advancement of the machinery, there is always a need for skilled operators, and Anchor has been very lucky through the years to have a good group of staff. The family tradition at the company’s core has spread to its employees, many of whom have fathers, siblings or other relations in the operation.
“We look for solid labourers whom we feel have potential to become an operator, then get them into the required training and schooling to become an operator,” he said.
Automation is helping shape the next generations of operators and changing how drills and other equipment are run, Speakman noted.
“It’s almost like a video game – a lot of them have joystick controls and monitors, so you are constantly monitoring the operation rather than the old-school way of listening for the machine to make the grunts and groans that it would make if there were trouble,” he said. “It’s much easier to run and doesn’t let you overtax it.”
Safety is a big aspect of the operation as well – and has to be for any construction company.
“If it’s not a focus, that company shouldn’t be in business,” Speakman said. “We start our day with a pre-job safety talk, and continue through the day with a job hazard analysis; we welcome input from any employee.”
Similar to the drilling side, hydraulic machines and larger equipment have moved in to the pile driving sector, though it continues to remain one of the more simple operations on a construction site.
“Pile driving is one of the oldest forms of construction, and it really hasn’t changed too much over time,” Winter said.
What has changed is the way in which pile driving contractors must work within the constraints of the ever-changing urban landscape. More restrictions on noise mean more challenges for the operation, noted Speakman.
“There are so many restrictions with regards to noise and vibration concerns. The density of Toronto doesn’t really allow for a lot of pile driving to take place,” he said. “We don’t go around damaging structures by pile driving, but there is nobody here who would say it’s not a nuisance.”
Today, pile driving is often used more on large infrastructure works such as sewage treatment plants, bridges and other large projects in less crowded spaces, while hydraulic drilling is used in other areas.
With a skilled staff and extensive array of equipment, it’s no surprise that Anchor Shoring has tackled many difficult jobs in the Toronto area – and, in some cases, very big jobs in more ways than one.
The Zone 1 watermain was a recent construction project in Oakville, just outside Toronto. A major project for the region, the proposed construction method required an entry shaft to be constructed to allow for a tunnel boring machine to be extracted. The problem: the shaft was huge, deep and had to be bored through Ontario bedrock.
“The client needed a shaft that was 150 feet deep, and fifteen and a half feet in diameter – and we drilled it, as opposed to conventionally shoring something and going in with a small excavator and crane, which would cause the shaft to be much larger in diameter,” Winter said. “The client really liked the solution we provided because it saved time and money.”
Anchor brought in a Liebherr LB 44 drill rig for the two-month project, which was the largest diameter hole the company had ever done.
“The biggest we had drilled prior to that was a 12-foot diameter – it doesn’t sound like the extra three and a half feet is much bigger, but the tooling required and the setup of the machinery is on a scale, and this was roughly doubled,” Speakman said. “We needed a police escort to move the auger – it was wider than the lane of traffic.”
As for the shaft itself, the depth was such that when Anchor’s team was drilling towards the bottom, it took seven minutes to bring the auger back up for soil removal, Speakman noted.
With the advancement of the machinery, there is always a need for skilled operators, and Anchor has been very lucky through the years to have a good group of staff. The family tradition at the company’s core has spread to its employees, many of whom have fathers, siblings or other relations in the operation.
“We look for solid labourers whom we feel have potential to become an operator, then get them into the required training and schooling to become an operator,” he said.
Automation is helping shape the next generations of operators and changing how drills and other equipment are run, Speakman noted.
“It’s almost like a video game – a lot of them have joystick controls and monitors, so you are constantly monitoring the operation rather than the old-school way of listening for the machine to make the grunts and groans that it would make if there were trouble,” he said. “It’s much easier to run and doesn’t let you overtax it.”
Safety is a big aspect of the operation as well – and has to be for any construction company.
“If it’s not a focus, that company shouldn’t be in business,” Speakman said. “We start our day with a pre-job safety talk, and continue through the day with a job hazard analysis; we welcome input from any employee.”