Contractor finds Champion C60 motor graders provide ideal solution
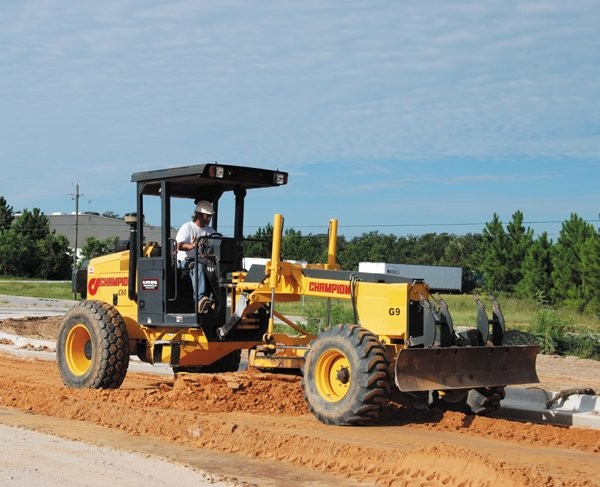
Floyd Brothers Construction specializes in building new parking lots from scratch, including all infrastructure and site work, beginning with earthmoving and site preparation, laying of the underground utilities, putting down the base and curbs and gutters, and then finish grading and paving. It’s a full-scale operation that requires the right kind of dependable and durable equipment to get the job done. After experimenting with a variety of graders over the years, including small tandem machines, the Floyd brothers settled on single axle Champion C60 Motor Graders to get the job done right, on time and within budget. Today, they have six of these units in operation.
“Our Champion C60 Graders are long enough to give us the required grading on the parking lots we construct. They’re also compact and mobile enough to let our operators maneuver the tight turns they need to make around curbs and islands when they are doing finish grading,” says Sam Floyd. “We prefer the single axle because when you twist with one axle versus two you have much less stress on the framework of the machine and it enables the operator to articulate the grader comfortably resulting in smoother grade work. For about 90% of the work we do, our operators would rather use the C60 model than the larger graders any day. The C60 single axle model is the perfect fit for our type of work.”
One option that all of their Champion C60 Motor Graders come with is Diamond Tread on their tires, which provides better “cleating” on the sandy subgrades in the Pensacola area. The Diamond Tread enables the graders to track better and it leaves a smaller footprint than regular tractor tires. “We’re one of the few regions that use this type of subgrade for grading and it’s a good case of knowing the nature of the job well enough when you’re specing your equipment. The Diamond Tread works best with our type of application” says Tim Floyd.
“Blue-top Operators” Love Their Champion C60 Graders
Most of the company’s motor grader operators are “blue-top operators” with years of experience on graders of all sizes. According to the Floyd brothers, their operators can switch effortlessly between the company’s larger graders and the Champion C60 Series models because of the industry standard controls on all Champion Graders. “Some of our grader operators come from other companies where there were only big graders. But once they get into one of our Champion C60 Graders, they realize it is a compact grader with a big grader feel,” says Tim Floyd.
“Our guys really like the visibility and articulation on the C60 Graders,” says Sam Floyd. “They get the finish they want faster and easier. As a result, all six of our C60 machines are running every single day. Our larger graders are now mostly used only for large roadwork applications.”
“In regard to cost versus production, our C60s have definitely proven themselves to be much more cost efficient than our larger graders,” says Tim Floyd. “With their single axles and big tires, the Champion C60 Graders really are our workhorses. They just run and run and run and never give us any problems.”
Floyd Brothers Credit McCoy for Success of Champion C60 Graders
The Floyd brothers bought their first Champion Motor Grader in 1995 from Herman McCoy, Branch Manager at Joe Money Machinery in Pensacola and a long-time fixture in the local heavy equipment business. Thirteen years later it still works everyday alongside the other machines they have bought since then – the latest being last year. The Floyd brothers credit McCoy with having drawn their attention to the Champion C60 model as the right piece of equipment for their parking lot construction application.
“Herman came to us and said ‘Guys, I’m going to put a single axle Champion C60 on demo here and I want you to give it a try. I think you’re going to be pleased with it,’” recalls Sam Floyd. “We weren’t sure about it at first, but after the demo, he sold us on it, and we’ve never looked back. Herman’s been great. He has a wealth of experience and knowledge of construction equipment and we’ve developed a lot of respect for him over the past thirteen years.”
“Herman has been more than just a sales representative to us,” says Tim Floyd. “We have developed a personal relationship with him and we often turn to him for advice on all of our equipment.”
Herman McCoy recalls how his knowledge of the Champion product line and of the parking lot application the Floyd brothers had in mind convinced him that the single axle C60 was their right equipment choice. “I knew this machine was the right fit for what these boys had in mind in terms of length, blade down pressure, maneuverability and cost” says McCoy. “It’s a well built compact grader with big grader features and durability.”
“We’ve tried other small graders and various attachments on skid steers and wheel loaders, but without much success,” says Tim Floyd. “Now if we’re going to get a grader, it’s going to be a single axle Champion C60.”
“Our grandfather and father were both in the earthmoving business, so we’ve been around earthmoving equipment all our lives. We know a winner when we see one – our Champion C60 Motor Graders are definitely winners,” says Sam Floyd.
About Champion
Champion engineering and manufacturing, based in Charlotte, NC, are dedicated to the production of compact and Production Class motor graders that assure customers of the same productivity and quality standards they expect from the best in full-size construction machinery. The Champion line-up now includes seven basic models with operating weights from 12,000 to 24,000 lbs., featuring the full range of single-axle, tandem and all-wheel 4x4 and 6x6 drive systems. Champion continues to develop a growing range of specialized equipment for the road maintenance and paving industry.