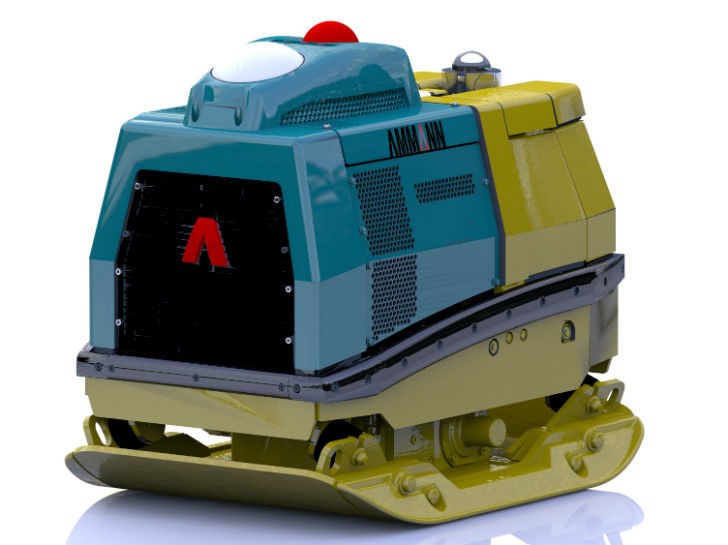
At Bauma 2016 Ammann presented the latest innovation within its range of compaction equipment. With the prototype of the first autonomous vibratory plate, Ammann gives its visitors a glance at the vibratory plate of tomorrow.
Operators of construction equipment are regularly exposed to wind and weather, as is expected. But operators of hand-held vibrating equipment, including plate compactors, also face elements such as exhaust emissions and vibration forces.
Despite these challenges, a qualified operator is essential to the success of the compaction project. The machines provide proper power, but the operator’s performance and attention to detail remain crucial to success.
That could be changing with the introduction of autonomous plate compactors. Autonomous vacuum cleaners and lawn mowers are on the market and gaining in popularity. The autonomy of vibrating plates is a logical next step – and a step Ammann is taking.
However, when compared to vacuum cleaners and lawn mowers, an autonomous vibratory plate raises considerable challenges. Among them:
- The materials and grade of the surface to be compacted vary from one site to the next
- Wires or fencing that could guide the autonomous plate are not desirable on building sites
- A specific compaction pattern must be developed to ensure quality compaction and also limit the fuel consumption given the autonomous compactor would be powered by a combustion engine
- The hydraulic or mechanical drive of the vibratory plate requires a technically more complicated mechatronic solution
The advantages of such a solution are nevertheless obvious. First, the autonomous vibratory plate provides significant cost savings for the contractor. While achieving compaction performances that equal heavy soil compactors, these plates use a fraction of the fuel. In addition, the CO2 emissions are reduced. The automation also eliminates operator errors.
How does the Ammann Prototype work?
An electro-hydraulic control, based on an existing remote-controlled vibrating plate, the Ammann APH 1000 TC, has been developed. In "Teach In" mode, the operator uses the remote control to navigate the plate along the borders of the area to be compacted. This is essentially setting the boundaries for the plate compactor. There is a confirmation process to ensure proper location. The number of vertices is not limited and the machine automatically detects the closed border. After clicking the "Run" button, a working strategy is calculated and the field is compacted strip by strip. Here, the control of a highly accurate GPS system is supported by an electronic compass and collision detection. Deviations of the GPS system are compensated by an overlap of the passes to ensure all areas are compacted sufficiently.
The prototype of the world’s first autonomous vibratory plate is a significant step for the compaction industry. The prototype proves that compaction equipment of the future can eliminate exhaust emissions and vibration to the operator while also providing cost savings to contractors, too. All this while providing great compaction quality.