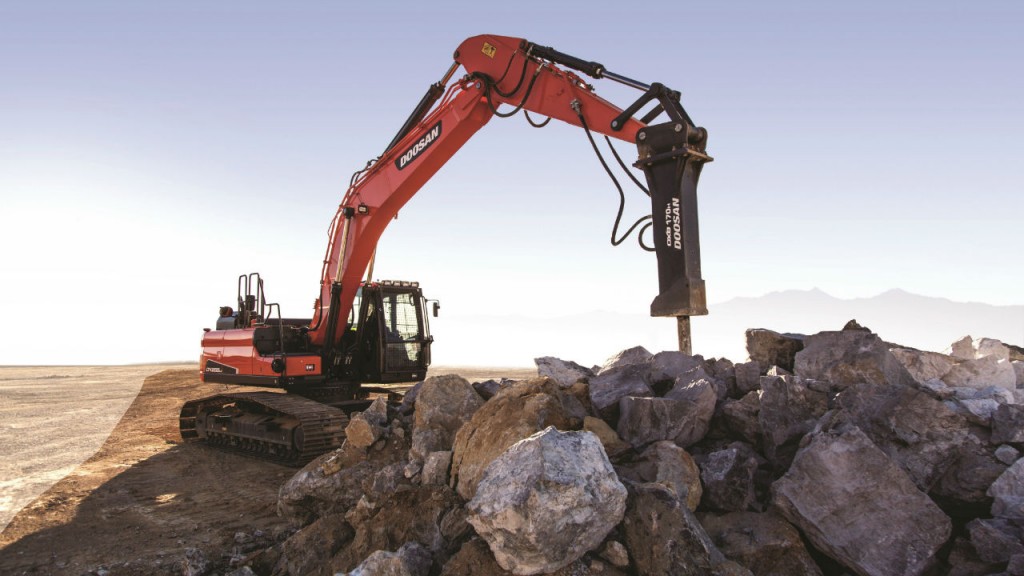
Excavator-mounted hydraulic breakers are an ideal attachment to help break rock, concrete, asphalt and other construction and aggregate materials. However, to achieve long-lasting attachment performance, routine maintenance needs to be top of mind.
A lack of routine maintenance can easily derail a project, costing you valuable time, money and potentially decreasing the attachment’s lifespan. By following these six tips outlined by Lee Smith, Doosan attachment product specialist, you can get optimal performance and life out of your heavy-duty hydraulic breaker.
Tip No. 1: Complete a visual inspection
Although it only takes a few minutes to visually inspect a hydraulic breaker for wear and tear, many operators overlook this step. A visual inspection should be completed each time the breaker will be used to help identify any worn or damaged components and prevent unexpected downtime.
“Daily visual checks can give an early look at worn items that can lead to potential failures down the road,” Smith says. “Check hydraulic hoses, the breaker shell, attachment pins, tool retainers and locks, and the tool point, for any cracks or gouges.”
Tip No. 2: Use the correct maintenance tools
Many breaker manufacturers provide a specialized check tool to measure the breaker’s lower bushing, top angle of the breaker tool and retaining pins. “Using this maintenance tool for its recommended checks will decrease the likelihood of early component failure,” Smith says.
The first step to using the maintenance tool is removing the retainer pins and breaker tool. Since you have the breaker tool removed, it is a good opportunity to give it an inspection for any cracks and use the maintenance tool to check the top angle. Also, check the retainer pins for wear and/ or damage.
Next, check the breaker’s bushing. “The maintenance tool is inserted into the bushing, and if it can be turned flat so that it fits end-to-end inside the bushing, the bushing needs to be replaced,” Smith says. “This simple check takes approximately 15 to 30 minutes and should be conducted once a week or every 50 hours of attachment use.”
“Any wear on the bushing can affect tool performance and should not be overlooked,” Smith says. “Bushing wear will allow front-to-back play in the breaker tool and can cause misalignment to the piston.”
Tip No. 3: Examine hydraulic hoses
Hydraulic hoses from the excavator should be the correct length and always be routed properly to help decrease wear and potential downtime. According to Smith, hoses that are short in length restrict attachment extension. On the flip side, hoses longer in length can catch or become disengaged on rebar and other debris. Doosan breakers, for example, come with standard hydraulic hoses that are the correct length for each of their machines to make installation easy and maximize operating time and hose protection.
Tip No. 4: Grease the attachment
Greasing the hydraulic breaker is the most important maintenance item because it lubricates and clears the tool bushing area of debris. Check that you are using the proper grease recommended by the breaker manufacturer.
As an example, Doosan recommends for their breakers a No. 2 lithium-based grease with three percent moly rated to 500 degrees Fahrenheit to help prevent metal-on-metal contact. Compared to standard lubricants, the grease is made for higher temperatures and remains between the steel and bushings at higher temperatures, providing for better and longer-lasting lubrication.
Greasing can be done manually or via an automatic greasing system. If you are using a hydraulic breaker that needs to be manually greased, make sure to follow manufacturer recommendations – typically every 1 to 2 hours – to reduce buildup, tool wear and bushing wear.
Applications and conditions can affect how often you need to grease. When the tool is penetrating material and making longer movements, it will need more frequent greasing than if it is doing impact breaking. Also increase the greasing in dusty conditions.
Some manufacturers feature an automatic lubrication (greasing) system for their hydraulic breaker models that delivers a constant flow of grease and eliminates manual greasing intervals. According to Smith, the lubrication system can be mounted on the breaker cradle directly or a larger tank can be machine mounted. The automatic system can save you labour-intensive time, save money down the road, and help to avoid over-greasing the hydraulic breaker.
Tip No. 5: Utilize the right tool point
Matching the tool point to its respective application can significantly maximize jobsite production and extend the breaker’s life.
Tool points include:
Moil tool point – for concrete demolition and breaking soft, nonabrasive rock.
Chisel tool point – various types of chisels are available for different materials, such as nonabrasive tough rock or concrete; abrasive hard rock; and nonabraisve, very soft rock. The chisel tool point provides more breaker control when being used for general excavation or cutting concrete for trenching.
Blunt tool point – easily breaks and fractures large pieces of concrete or block in heavy construction applications. Can also be used to break boulders.
Pyramidal tool point – used for breaking hard, abrasive material in demolition. Also suitable for breaking soft, nonabrasive material, such as sedimentary rock.
Tip No. 6: Inspect nitrogen pressure
Determining the proper nitrogen charge pressure depends on the application and outside working temperature, Smith says.
“The nitrogen level for breaking rock should be different than breaking concrete in a parking lot,” he says. “The outside temperature also adds another variable. The attachment’s Operation and Maintenance Manual gives you the recommended nitrogen pressure setting for your application and working temperature.”
By following these hydraulic breaker maintenance tips, you can better utilize your attachment on multiple jobsites and help extend its life. Be sure to complete the recommended maintenance schedule for your hydraulic breaker. Catching any obvious concerns during a routine visual check can help reduce unnecessary downtime.