Going mobile to manage equipment
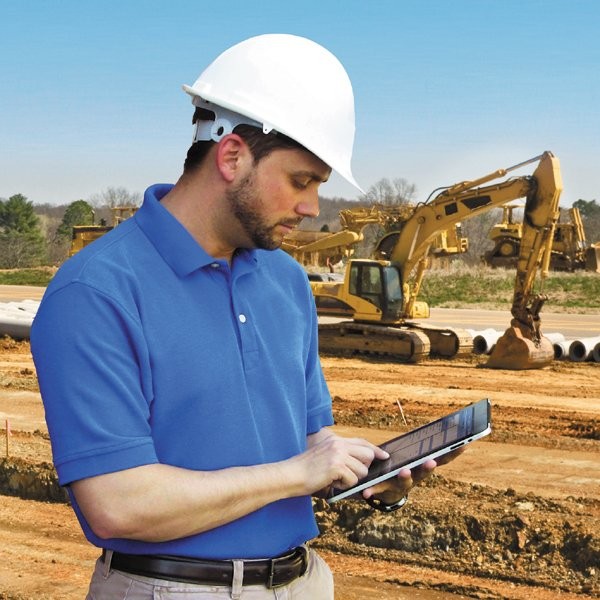
There is no doubt that equipment is one of the largest cost centres for most contractors. With often hundreds of thousands to millions of dollars worth of bulldozers, cranes, excavators, graders, skidders, and so on, construction companies have been driven in recent years to manage this major capital expense more efficiently.
Making the initial financial investment in equipment is just the beginning of what must be a well managed operation in order to be optimally profitable.
Contractors must make sure that equipment is on a jobsite when needed and ensure it doesn’t sit idle when it could be used elsewhere.
Equipment operators must be trained so that they use the piece properly and efficiently and comply with environmental and safety regulations. To maximize the value of equipment, contractors must ensure it’s maintained, making preventative maintenance an essential priority to prevent costly problems and downtime.
Furthermore, equipment management can be an important profit center for a contractor that carefully tracks usage and cost of ownership and bills costs to jobs as appropriate.
Linking it all together
Correctly managing equipment can be extremely complex and can significantly impact a company’s bottom line. There are many software solutions that help simplify the equipment management process but a solution that provides seamless workflow between estimating, job costing, financials, and project management empowers a contractor to truly maximize equipment investments.
A complete construction management solution can handle the entire project lifecycle, allow contractors to manage equipment and utilization, and define and track maintenance schedules and procedures, while tracking the cost of ownership.
Contractors can leverage the value of a complete solution to gain control over the capital intensive aspect of their business, as well as minimize the costs associated with equipment and keep their equipment active at jobsites. With a true picture of costs against budget, they can also manage their equipment as a company profit centre.
The value of mobility
With recent advances in mobile technology, equipment and project managers, and other appropriate team members, can increase their operational efficiencies by having access to real-time data while working on the jobsite. The arrival of the iPad has made informed, on-the-jobsite decisions easier and more convenient than ever. The device is not only easy enough for a computer novice to use, it also offers the sophistication needed for contractors to access detailed data no matter if the person is working in the office, at a jobsite, at an equipment storage facility or on the road.
This mobility and real-time access can be a true asset in turning equipment into a profit center. With a complete construction management software solution and mobile application, contractors can easily pull or enter data using an iPad to, for example, record equipment location and utilization information to the appropriate project and cost code.
And, with one central location for all the related data (such as receipts, warranties, insurance certificates, repair bills, and pictures), the accounting department can apply cost of ownership to each piece of equipment through accounts payable, journal entries, and payroll, using cost codes to breakdown each expense.
The mobility aspect of a complete, all-in-one software solution also enables contractors to minimize costs associated with equipment repairs and keep their equipment active at their jobsites. Having real-time information on the condition of the equipment, a maintenance schedule, alerts notifying when service is required, and more, can help project managers and equipment managers make sure that important maintenance is done in a timely and cost-effective manner.
A powerful combination
Contractors that leverage the combined power of a complete construction management software solution with mobile access from an iPad, will reduce downtime, prevent costly repairs, maximize the profit of every project, and improve the financial stability of their business.