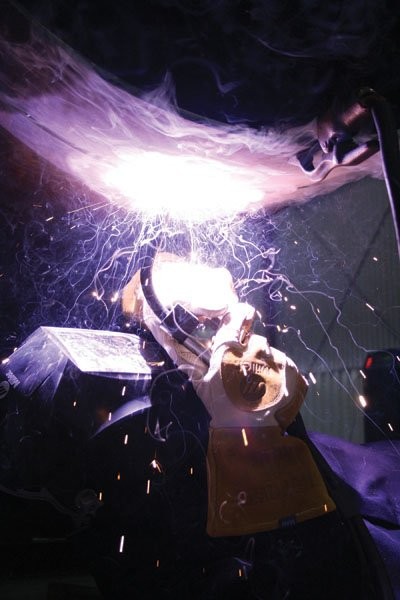
by Roger Hobrock and Derick Railling
There are two ways to reduce pipeline costs as it relates to the pipe itself: reduce the weight of steel used in its construction and/or increase the pressure tolerances so it pumps a greater amount of material. These factors have led pipeline contractors to transition to the use of high-strength steels up to Grade X100.
These high-strength steels pose new challenges to the welding process: filler metals must match or exceed the higher tensile strengths while also having lower hydrogen content. High-strength steels feature a low carbon base and are more prone to hydrogen-induced cracking. Cellulosic Stick electrodes used for welding low-strength steels possess too high of a hydrogen content (typically 16 ml per 100 g) to make them viable options for welding Grade X70 or higher steel.
To address these issues, a shift is taking place from Stick welding (SMAW) to Self-Shielded Flux Cored welding (FCAW-S). While Stick welding is still almost universally specified for root passes (although new Metal Cored wire and Miller’s Regulated Metal Deposition (RMD) processes are making gains there, too), Self-Shielded Flux Cored welding offers substantial advantages in productivity and quality.
Advantages of self-shielded flux cored welding
As with Stick electrodes, Self-Shielded Flux Cored wires provide shielding of the weld puddle, making it suitable for welding in the windy and dirty environments encountered in pipeline welding applications. While it requires additional equipment considerations (detailed further in the article), and may require re-qualifying certain joints and applications, the process offers noticeable advantages over Stick welding in a number of areas:
• Lower Hydrogen Content: Arguably the most important benefit, Self-Shielded Flux Cored wires designed for onshore pipeline applications provide the high-strength properties required, while also meeting the low hydrogen content standards required to reduce hydrogen-induced cracking.
• Increase in Speed, Deposition Efficiency: While quality is paramount, Flux Cored welding typically allows for faster travel speeds and offers greater filler metal deposition efficiency as compared to Stick electrodes. A standard E6010 or E7010 Stick electrode offers 50 to 65 percent deposition efficiency while a E71T8-Ni1 J H8 Flux Cored wire like Hobart Brothers’ Fabshield 79T8 offers 78 to 87 percent deposition efficiency.
• Increased Control of Arc: With the addition of voltage-sensing wire feeders and dual schedule capabilities associated with Flux Cored wire feeders and guns, the welder has more control over the precise performance of the welding arc.
• Easy to Operate: The Flux Cored process allows for relatively easy operator training. Variables such as pre-heat and interpass temperatures, along with the overall welding parameters (amperage, voltage, etc.), must be carefully monitored when welding high-strength pipe. Those features alone make welding this material precarious, so having a welding process that is easy to use minimizes additional variables involved with training.
Self-shielded flux cored filler metal
Filler metals used to weld high-strength pipe must meet or exceed the material’s mechanical and chemical property requirements, and provide the ductility to mitigate instances of cracking. They also need to compensate for the extreme temperatures to which pipelines are typically subject, as the impact of thermal expansion or contraction, frost and other environmental loadings can easily damage steel and the welds.
To date, several classifications of Self-Shielded Flux Cored wires have proven successful for welding high-strength pipelines worldwide. These wires have been specially formulated to generate low levels of spatter and create an easily removable slag to speed inter-pass and post-weld clean up.
Because they require no shielding gas, they can eliminate the time and need for setting up shielding tents to protect gas coverage. In addition, these wires provide good vertical-down capabilities and offer higher deposition rates than Stick electrodes to help improve productivity.
Available Self-Shielded Flux Cored wires for welding high-strength pipelines include:
• E71T8-Ni1 J H8: This all-position wire has been designed for onshore transmission pipelines composed of Grade X70 (and below) pipe and provides high-impact toughness at low temperatures. It offers a tensile strength of 78 ksi in the as-welded (AW) condition and creates welds with low diffusible hydrogen levels (5.45 ml/100 g). The wire’s unique formulation offers excellent weld puddle control, particularly when welding from the 4 o’clock to 7 o’clock position.
• E81T8-Ni2 J H8: This wire can be used for fill and cap passes on pipeline projects constructed from Grade X80 (and below) pipe. It provides high tensile strength (94 ksi) and low CVN impact properties (as low as 96 ft.lbs. at -40 degrees Fahrenheit/Celsius), as well as excellent ductility.
• AWS E91T8-G H8: In addition to offering relatively low diffusible hydrogen content (6.2 ml/100 g), this all-position wire provides a tensile strength of more than 113 ksi, as well as excellent low-temperature impact strengths (44 ft.-lb. at -40 degrees Fahrenheit/Celsius). This wire has been designed for use as an overmatch on Grade X80 pipe and also offers good ductility.
• AWS E111T8-G H8: Used for welding Grade X100 pipe and as an overmatch on Grade X80 steel, this wire also operates in a manner similar to the aforementioned wires but offers much higher tensile strengths.
Equipment considerations
Stick and Flux Cored welding can be performed with the same engine-driven welding generators pipeline welders have used in the past, although there are newer machines (Miller’s Big Blue 350 PipePro, for example), that feature enhanced outputs that optimize performance for Flux Cored welding. New dual operator systems (such as the Big Blue 700 Duo Pro) provide two pipeline-quality arcs suitable for Flux Cored welding that allow two welders to work off the same machine without interaction or interference between the arcs. This helps reduce fuel costs, lowers total ownership costs (compared to two separate machines), and even allows a welder to parallel the two independent arcs for running larger wires.
There are additional equipment considerations that have been deterrents in the past: a Self-Shielded Flux Cored gun can be more complicated than a stinger used in Stick welding, the wire feeder provides an additional piece of equipment to own and maintain, and controlling things like amperage and wire feed speed are perceived to be more difficult than with a Stick electrode. Equipment manufacturers have taken steps to improve the overall quality, simplicity and productivity of these products. Advancements include:
• Wire Feeders: Once large and clunky, new wire feeder designs – like that of Miller’s SuitCase X-TREME 8 HD – have become more compact and reliable. Tight-sealing polypropylene cases keep out dirt and contaminants. High-torque motors handle both large and small diameter Flux Cored wires, and provide more consistent feeding. Digital meters capable of displaying both voltage and amperage while welding helps improve welding accuracy. Voltage-sensing models offer precise arc control.
• Self-Shielded Flux Cored Guns: Self-Shielded Flux Cored guns have been made substantially lighter and more ergonomically friendly than past models. Advances to guns such as the Bernard PipePro Dura-Flux gun include internal trigger leads that won’t get caught on surrounding equipment, replaceable liners, and rotatable Hi-Viz necks that provide improved visibility to the weld puddle. Most importantly, the dual schedule functionality gives welders the opportunity to adjust wire feed speed right at the gun.
• Wireless Remote Controls: Whether Stick or Flux Cored welding, new wireless remote controls extend the work envelope up to 300 feet from the power source. Typical corded remotes only extend to 90 feet. Digital displays on wireless remote controls further give welders and welder’s helpers a precise knowledge of their machine’s settings.
As for meeting the overall demands of building high-strength pipelines, it is likely that the shift to the Self-Shielded Flux Cored process will continue as contractors seek to complete projects faster and for less cost. It is equally likely that filler metal and welding equipment manufacturers will be challenged to build on this technology and offer even more solutions to meet the strict welding requirements of high-strength pipe and provide these contractors with an increasingly competitive edge.
Roger Hobrock is director, North American transmission pipelines, Miller Electric Mfg. Co. Derick Railling is product manager, global onshore pipeline division, Hobart Brothers Company.