Engine manufacturers take multiple approaches to meeting Tier 4 Final emissions standards
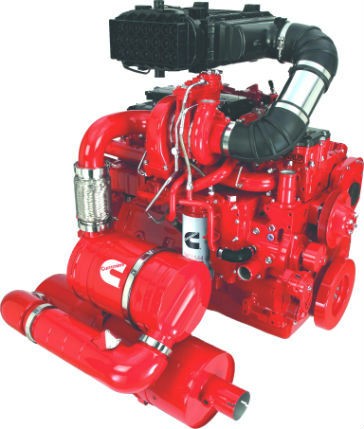
Implementing new standards for diesel engine emissions has been a priority of the U.S. Environmental Protection Agency (EPA) for the past two decades.
Emanating from the general principles of the 1955 U.S. Clean Air Act, a federal law designed to control pollution levels, the EPA rolled out a system of successively more stringent phases of emissions reduction, or “tiers” that must be followed by diesel engine manufacturers and makers of construction equipment used in non-highway applications. Diesel emissions from on highway vehicles including trucks and buses had been regulated prior to the introduction of EPA regulation of off-road construction equipment in the mid-1990s.
Beginning in 1996, this tiered system has now gone through six stages – Tier 1, Tier 2, Tier 3, Tier 4, Tier 4 Interim and Tier 4 Final. In January 2011, the EPA required off-road equipment manufacturers to use diesel engines that comply with Tier 4 Interim emissions regulations, which apply to non-road diesels 175 horsepower or greater. This is the power range used in heavier equipment, such as excavators, loaders, cranes and mining trucks. Stationary power units became subject to Tier 4 requirements when the EPA issued standards for compression-ignition engines in 2006.
The first phase of Tier 4 Final became effective on January 1, 2014 and applied to off-road diesel engines from 175 to 750-hp. Engines in the second phase, 75 to 174-hp range and more than 750 horsepower, became subject to Tier 4 Final regulation in January 2015. Manufacturers of engines 25-hp and below have had to comply with Tier 4 emissions standards since 2008, while those between 25 and 75-hp were placed under Tier 4 regulation in 2013.
While Tier 4 is essentially an EPA-driven program, in 2011 Environment Canada aligned Canadian emission standards with U.S. EPA Tier 4 standards for non-road engines. These standards came into effect in 2012 and apply to engines manufactured that year and newer. Europe follows a similar system to the EPA, with Stage I to V regulations.
In-cylinder treatment
Tier 4 regulations address emissions of carbon monoxide and hydrocarbons (unburnt fuel), but their primary purpose is to limit the amount of tailpipe emissions in the form of particulate matter (PM) and nitrogen oxides. Particulate matter, the “black soot” coming out of diesel engines, is especially harmful to human health since the tiny particles can lodge into the lungs and cause permanent damage. A 2013 study of nine European countries showed a direct correlation between exposure to diesel particulate matter and rates of lung cancer.
Nitrogen oxides, produced from the chemical reaction of nitrogen and oxygen during engine combustion, are also harmful when inhaled, and are known to contribute to smog and acid rain.
It is important to note that while Tier 4 Interim was primarily aimed at reducing particulate matter in diesel exhaust, Tier 4 Final is more comprehensively directed at reducing PM, NOx and unburnt hydrocarbons. Between Tier 4 Interim and Tier 4 Final, it is estimated that NOx is reduced by some 80 percent, said Volvo Penta, a supplier of engines and power systems for marine and industrial applications.
In order to limit PM and NOx, engine manufacturers developed techniques, built into the combustion process, would reduce these pollutants. In-cylinder methods included modifications to the combustion chamber; fuel system refinement including common rail fuel injection; variable geometry turbo chargers (VGT); and exhaust gas recirculation (EGR).
The latter takes emissions from the combustion chamber, including NOx, PM and hydrocarbons, and reintroduces them into the combustion system so they can be burnt again. Controlling the temperature is key to reducing the formation of emissions, particularly NOx. Some engine manufacturers have therefore employed a cooled exhaust gas recirculation system (CEGR), whereby hot exhaust gases are run through a circulation system to lower the temperature of the combustion chamber and thereby reduce the formation of nitrogen oxides.
John Deere was the first engine manufacturer to commercialize cooled EGR and VGT technologies in off-highway applications, according to the company.
Exhaust after-treatment options
To reach the near-zero emissions levels required by Tier 4 Interim and Tier 4 Final, the engine manufacturers had to take another step in reducing emissions, and that is where exhaust after-treatment comes in. Over the last five years in North America most manufacturers have moved to selective catalytic reduction (SCR), which is either used alone to deal with NOx leaving the cylinder, or in combination with EGR.
“For the move from Tier 3 to Tier 4 Interim, some type of after-treatment system or EGR needed to be added. When Tier 4 Final emissions regulations were put into effect, all engine manufacturers required the addition of the after-treatment system, with most resorting to using a diesel particulate filter as well,” said Scania, the Swedish engine manufacturer.
With SCR a catalyst is positioned in the exhaust stream, that periodically sprays diesel exhaust fluid (DEF) – a combination of water and urea – to react with the nitrogen oxides in the exhaust and thus lower tailpipe emissions. To engine manufacturers, the main attraction of the SCR system is its ability to produce the desired performance and fuel economy for the design of the machine, while effectively treating what would be higher levels of emissions in the exhaust stream, said Allen Schaeffer, executive director of The Diesel Technology Forum, a non-profit organization that raises awareness of diesel engines, fuel and technology.
“Why are they using SCR? Because it provides the manufacturer with more flexibility in terms of delivering an engine that has as good or better fuel economy and other benefits for their customer,” Schaeffer told Heavy Equipment Guide in an interview.
Even though SCR requires equipment users to purchase diesel exhaust fluid in addition to diesel fuel (all of which since 2010 is now ultra-low-sulphur diesel – less than 15 parts per million sulphur), Schaeffer said most engine manufacturers see SCR as preferable to an after-treatment system that employs a series of filters or catalysts: “SCR is really one of the leading emissions control technologies out there for off-road Tier 4 Final machines,” he said.
Drastic reductions in the level of particulate matter required for Tier 4 engines, particularly the two most recent standards, Tier 4 Interim and Tier 4 Final, have also led engine makers to use two devices commonly used for capturing and reducing particulate matter in the exhaust stream: the diesel particulate filter (DPF) and the diesel oxidation catalyst (DOC).
A DPF traps tiny particles through a combination of filtration mechanisms, while the DOC, as the name suggests, promotes oxidation of several exhaust gas components, rendering them inert. The DPF is known to be highly efficient, reducing PM by over 90 percent, and has become the most effective technology for controlling diesel particulate emissions, according to DieselNet, an online information service covering diesel engines, emissions and fuels.
Tier 4 technology variations
Looking at all these emission-reduction technologies, Schaeffer said there is a high degree of variability in terms of which ones engine manufacturers employ to reach the required reduction in NOx and PM. For example, some may use SCR alone, or perhaps in combination with a cooled EGR system, without the use of a DOC or DPF. Others may use only SCR or EGR, but add a filtration or oxidation after-treatment.
“There are some manufacturers that have very high horsepower, large displacement engines that are not using exhaust after-treatment,” he said. “And then there are other manufacturers that have similar kinds of engines and technology and are choosing to use it.”
Cummins, for example, offers multiple after-treatment solutions to equipment OEMs that install its engines, rationalizing that an important starting point for introducing Tier 4 was to make the OEM installation transition as simple as possible, in terms of packaging, envelope size and electronic integration.
“This approach has proven to be a real advantage for equipment manufacturers as the emissions regulations have cascaded down the power bands to include smaller equipment where space constraints are more challenging,” said Kevan Browne, communications director at Cummins. The engine manufacturer also sought to make the transition easier by making its Tier 4 offerings “machine adaptive” to meet Tier 4 Final.
“We designed our Tier 4 Interim after-treatment as a modular system able to later incorporate SCR for Tier 4 Final,” said Browne. “For our mid-range engines, space was made available by replacing the diesel particulate filter with a smaller, simpler diesel oxidation catalyst system.”
Scania took a slightly different approach. In moving from Tier 3 to Tier 4 Interim, Scania redesigned their combustion chambers in combination with the added SCR system, rather than just solely add an after-treatment system without engine improvements to compensate.
“This resulted in greatly improved fuel economy, while at the same time reducing NOx and HC to required levels,” the company stated. “When Tier 4 Final emissions regulations were put into effect, the Scania strategy and after-treatment system was advanced into a more mature system, but remained mostly unchanged. Scania was able to meet the strict particulate demands without the addition of a DPF, unlike most other manufacturers.”
For Caterpillar, most of the changes to its off-road engines occurred during the Tier 4 Interim phase-in, with Tier 4 Final engine offerings largely looked upon as improvements to existing Cat technologies. “The result: engine platforms that are virtually unchanged, yet meet today’s stringent emissions standards,” says a video overview of Caterpillar’s Tier 4 engine technology, which centres around four “building blocks”: electronics, fuel systems, air management and after-treatment.
Engines smaller than the C13ACERT use a common rail fuel injection system, while the C13ACERT and larger employ the MEUI-C fuel injector first introduced in 2006. In both designs fuel is delivered in multiple shots as a fine mist, to burn fuel efficiently to reduce NOx formation and control soot formation. The Cat Clean Emissions Module includes a DOC and a DPF, contained in a single canister mounted on a support structure. An electronically-controlled regeneration system initiates regeneration automatically without operator involvement. An SCR system activated by diesel exhaust fluid is used in all Cat engines 175 to 750-hp.
To meet Tier 4 Interim requirements, John Deere took its Tier 3 PowerTech Plus engine platform with cooled EGR and added an exhaust filter, which consisted of a DOC and DPF to reduce particulate matter.
John Deere’s Integrated Emissions Control system encompasses different combinations of after-treatment and emissions reduction components. For Tier 4 Final, John Deere is currently offering three Integrated Emissions Control system configurations, in ranges of 48 to 74-hp, 75 to 154-hp, and above 125-hp.
“These tailored configurations provide an optimized solution that delivers responsive performance, reliable uptime and a low cost of operation,” said Craig Timmerman, product marketing manager, engines and powertrain, John Deere Construction & Forestry.
When Volvo Penta moved to Tier 4 Final, the company improved its SCR system which gave its engines greater NOx reduction, and added light cooled EGR. Volvo Penta says it has met or exceeded EPA standards without the use of a DOC or DPF. “Our Tier 4F SCR strategy is a proven, simple and efficient solution, with technology that has been used in on-highway trucks for 10 years,” said Shawn Sweet, vice president industrial sales, Volvo Penta of the Americas. “We have a simple package with no DPF, no DOC and no regeneration. This means the package is smaller, which makes it easier for the OEM to install and with less service components it’s easier and less expensive for the operator to maintain.”
Kubota’s Tier 4 Interim technologies featured cooled exhaust gas recirculation, a common rail system, multiple injection, and a “wall flow filtration system” that cleans the DPF after regeneration. In 2014 the Japanese engine manufacturer came out with four new engines with DOC-only after-treatment, in outputs from 48.9 to 73.2-hp, expanding its previous offerings using a DPF as the after-treatment device.
And finally, Perkins’ strategy for meeting the Tier 4 Interim regulations was through a combination of DOC/ DPF and exhaust gas recirculation, rather than SCR. However, at Intermat in 2012 the company came out with a range of four-cylinder Tier 4 Final engines that employ selective catalytic reduction without the use of a DPF. The idea was to minimize the cost to the equipment manufacturer of transitioning from Tier 4 Interim to Tier 4 Final. “By maintaining a high carryover of components from the previous Tier/Stage, keeping similar cooling packages and retaining compact dimensions for the engine envelope, Perkins has reduced the need for OEMs to undergo costly machine redesign,” Perkins stated at the time.
Operator factors to consider
When it comes to deciding which-tier machine to use for a given work detail, equipment operators have a number of factors to consider. These include the regulations behind the particular horsepower category, the power rating on the machine, the application and bid requirements.
Performance is usually the driving consideration, but the amount of power and torque generated by the engine needs to be balanced with the amount of fuel required for the job. Scania notes that fuel consumption is reduced by around 13 percent in a Tier 4 Final engine versus an earlier Tier 3 model.
But, while fuel savings are often touted as a benefit of Tier 4 Final engines – heavy-duty trucks, for example, made with new engine technology are five to eight percent more fuel-efficient than those made before 2010 – that advantage may be negated if the machine is working on a particularly demanding application and using a lot of diesel exhaust fluid.
“The machine that operates under heavy loads most of the time, like a wheel-loader material handling at a quarry, running eight hours a day dumping big buckets full of crushed rock into dump trucks, that is running a lot of cycles, is going to consume diesel exhaust fluid faster than a machine that works for four hours but then idles for three, four hours a day on average, or works a very light load, or is just transiting,” said Schaeffer. “So it’s very dependent and very difficult to generalize what the consumption is.”
What can also come into play, added Schaeffer, are the kinds of jobs a contractor is likely to bid on. Public works and P3 contracts are increasingly sensitive to environmental issues, so contractors with low-emissions fleets will have an advantage over contractors using earlier-tiered equipment. “It becomes part of the conversation in the bid process,” he said.
Browne, from Cummins, said operators have noticed Tier 4 engines to be cleaner and quieter than Tier 3 models, which is not surprising considering that Tier 4 machines emit 90 percent less PM and NOx.
Cummins’ Tier 4 engines also deliver faster torque to meet load demands, said Browne, and require less frequent refuelling due to cleaner, more-efficient combustion. And while some operators will see the need to refuel the DEF tank periodically as a negative, he said the fuel savings more than outweigh the cost of using DEF, at least for a Cummins Tier 4 Final-powered machine.
“So the message to operators is, boost your productivity, reduce your operating costs and lower your carbon footprint by moving forward to Tier 4 Final equipment,” he said.